A method for rapid slag formation in the tapping process of high-quality steel
A high-quality technology for the tapping process, applied in the field of steelmaking, can solve the problems of ineffective deoxidation of refining slag and rapid slag formation, and achieve the effects of improving product quality, improving molten steel quality, and improving metallurgical effects.
- Summary
- Abstract
- Description
- Claims
- Application Information
AI Technical Summary
Problems solved by technology
Method used
Image
Examples
Embodiment 1
[0031] In the production process of 42CrMo steel grade, the implementation of the method of rapid slag formation in electric furnace tapping includes the following steps:
[0032] Step 1: Control the tapping temperature at 1670°C in a 110t electric furnace;
[0033] Step 2: When the tapping amount reaches 35t, add pre-deoxidizer and alloy total about 3000kg through the alloy chute to the molten steel casting stream to realize the initial precipitation deoxidation and preliminary alloying of molten steel, and add lime 400-500kg through the alloy chute at the same time and pre-melting refining slag 300kg, the ladle bottom blowing argon is used in the tapping process, and the flow rate of the bottom blowing argon is controlled at 25-50Nm 3 / h;
[0034] Step 3: After tapping is completed and the liquid slag layer on the surface of the molten steel is completely formed, reduce the flow rate of the bottom blowing argon to keep the diameter of the exposed surface of the molten steel...
PUM
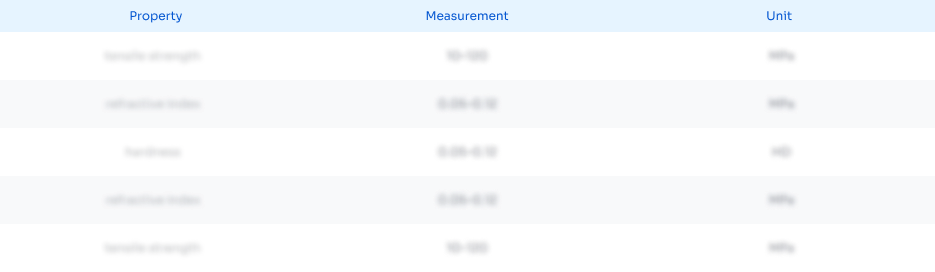
Abstract
Description
Claims
Application Information

- R&D
- Intellectual Property
- Life Sciences
- Materials
- Tech Scout
- Unparalleled Data Quality
- Higher Quality Content
- 60% Fewer Hallucinations
Browse by: Latest US Patents, China's latest patents, Technical Efficacy Thesaurus, Application Domain, Technology Topic, Popular Technical Reports.
© 2025 PatSnap. All rights reserved.Legal|Privacy policy|Modern Slavery Act Transparency Statement|Sitemap|About US| Contact US: help@patsnap.com