Nano-ceramic coating for thermal insulation of glass
A nano-ceramic and nano-ceramic powder technology, applied in fire-resistant coatings, polyester coatings, polyurea/polyurethane coatings, etc., can solve the problems affecting the actual effect and service life of heat insulation and energy saving, insufficient paint film adhesion, and film yield rate. Low problems, to achieve excellent optical transparency and heat insulation performance, to meet the effect of flexural resistance, strong high temperature resistance
- Summary
- Abstract
- Description
- Claims
- Application Information
AI Technical Summary
Problems solved by technology
Method used
Image
Examples
Embodiment 1
[0023] The preparation method of nano ceramic powder comprises the following steps:
[0024] 1) Calculated in parts by weight, weigh 50 parts of nano-zirconia, 30 parts of nano-silicon nitride, 2 parts of nano-titanium nitride and 1 part of nano-zinc oxide;
[0025] 2) Prepare the weighed ingredients into a suspension, then ultrasonically stir until uniform, then ball mill and mix uniformly on a ball mill, and vacuum dry to obtain raw material powder;
[0026] 3) Put the mixed raw material powder into a graphite mold, and prepare it by hot-pressing sintering process. The hot-pressing sintering temperature is 1460° C., the holding time is 10 hours, and pulverized to obtain nano-ceramic powder.
Embodiment 2
[0028] The preparation method of nano ceramic powder comprises the following steps:
[0029] 1) Calculated in parts by weight, weigh 60 parts of nano-zirconia, 20 parts of nano-silicon nitride, 5 parts of nano-titanium nitride and 3 parts of nano-zinc oxide;
[0030] 2) Prepare the weighed ingredients into a suspension, then ultrasonically stir until uniform, then ball mill and mix uniformly on a ball mill, and vacuum dry to obtain raw material powder;
[0031] 3) Put the mixed raw material powder into a graphite mold, and prepare it by hot pressing sintering process. The hot pressing sintering temperature is 1600° C., the holding time is 3 hours, and pulverized to obtain nano ceramic powder.
Embodiment 3
[0033] A nano-ceramic coating for glass heat insulation, calculated in parts by weight, comprising the following components:
[0034] 38 parts of water-based polyurethane, 12 parts of water-based alkyd resin emulsion, 7 parts of nano-ceramic fiber, 12 parts of potassium hexatitanate whisker, 8 parts of nano-ceramic powder of embodiment 2, 15 parts of nano-perlite, 4 parts of alumina fiber, 2 parts of ammonium acrylate dispersant, 2 parts of methyl cellulose, 0.6 part of polydimethyl aqueous polyurethane solution and 20 parts of water.
PUM
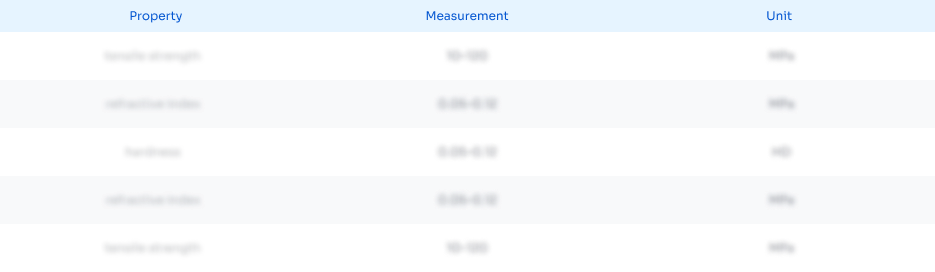
Abstract
Description
Claims
Application Information

- R&D
- Intellectual Property
- Life Sciences
- Materials
- Tech Scout
- Unparalleled Data Quality
- Higher Quality Content
- 60% Fewer Hallucinations
Browse by: Latest US Patents, China's latest patents, Technical Efficacy Thesaurus, Application Domain, Technology Topic, Popular Technical Reports.
© 2025 PatSnap. All rights reserved.Legal|Privacy policy|Modern Slavery Act Transparency Statement|Sitemap|About US| Contact US: help@patsnap.com