High-strength heat-resistant cable jacket material and preparation method thereof
A cable sheath, high-strength technology, used in rubber insulators, organic insulators, etc., can solve problems such as insufficient heat resistance and strength, and achieve the effect of improving mechanical strength, excellent heat resistance, and ensuring vulcanization effect.
- Summary
- Abstract
- Description
- Claims
- Application Information
AI Technical Summary
Problems solved by technology
Method used
Image
Examples
Embodiment 1
[0031] The high-strength heat-resistant cable sheath material of this embodiment is made of the following raw materials in parts by weight: 40 parts of nitrile rubber, 15 parts of EPDM rubber, 10 parts of chlorosulfonated polyethylene, 2 parts of vulcanizing agent, two 10 parts of tetramethylthiuram sulfide, 5 parts of benzoyl peroxide, 3 parts of ethylene-vinyl acetate copolymer, 2 parts of zinc stearate, 3 parts of active zinc oxide, N, N'-m-phenylene bis-hormone 2 parts of imide, 1 part of highly dispersed white carbon black, 2 parts of modified sepiolite powder, 3 parts of nano silicon dioxide, 0.5 parts of hydroxyl silicone oil, 3 parts of calcined metakaolin powder, 2 parts of modified phenolic resin, three parts 1 part of antimony oxide, 3 parts of magnesium hydroxide, 0.5 part of accelerator, 0.4 part of antioxidant, and 0.3 part of plasticizer.
[0032] Wherein, the vulcanizing agent is a mixture of sulfur, vulcanizing agent DCP and auxiliary vulcanizing agent TAIC in...
Embodiment 2
[0046] The high-strength heat-resistant cable sheath material of this embodiment is made of the following raw materials in parts by weight: 60 parts of nitrile rubber, 30 parts of EPDM rubber, 20 parts of chlorosulfonated polyethylene, 5 parts of vulcanizing agent, 20 parts of tetramethylthiuram sulfide, 10 parts of benzoyl peroxide, 6 parts of ethylene-vinyl acetate copolymer, 4 parts of zinc stearate, 8 parts of active zinc oxide, N, N'-m-phenylene bis-hormone 5 parts of imide, 3 parts of highly dispersed white carbon black, 4 parts of modified sepiolite powder, 5 parts of nano silicon dioxide, 1 part of hydroxyl silicone oil, 5 parts of calcined metakaolin powder, 4 parts of modified phenolic resin, three parts 3 parts of antimony oxide, 6 parts of magnesium hydroxide, 1.5 parts of accelerator, 00.8 parts of anti-aging agent, and 0.7 parts of plasticizer.
[0047] Wherein, the vulcanizing agent is a mixture of sulfur, vulcanizing agent DCP and auxiliary vulcanizing agent TA...
Embodiment 3
[0061] The high-strength heat-resistant cable sheath material of this embodiment is made of the following raw materials in parts by weight: 50 parts of nitrile rubber, 22 parts of EPDM rubber, 15 parts of chlorosulfonated polyethylene, 3.5 parts of vulcanizing agent, two 15 parts of tetramethylthiuram sulfide, 7.5 parts of benzoyl peroxide, 4.5 parts of ethylene-vinyl acetate copolymer, 3 parts of zinc stearate, 5.5 parts of active zinc oxide, N, N'-m-phenylene bis-hormone 3.5 parts of imide, 2 parts of highly dispersed white carbon black, 3 parts of modified sepiolite powder, 4 parts of nano-silica, 0.7 parts of hydroxyl silicone oil, 4 parts of calcined metakaolin powder, 3 parts of modified phenolic resin, three parts 2 parts of antimony oxide, 4.5 parts of magnesium hydroxide, 1 part of accelerator, 0.6 part of antioxidant, and 0.5 part of plasticizer.
[0062] Wherein, the vulcanizing agent is a mixture of sulfur, vulcanizing agent DCP and auxiliary vulcanizing agent TAIC...
PUM
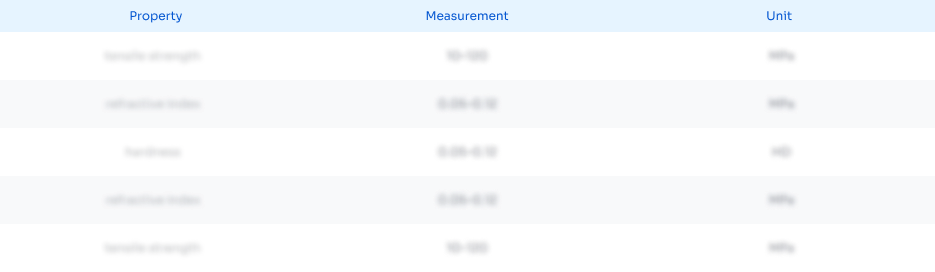
Abstract
Description
Claims
Application Information

- R&D Engineer
- R&D Manager
- IP Professional
- Industry Leading Data Capabilities
- Powerful AI technology
- Patent DNA Extraction
Browse by: Latest US Patents, China's latest patents, Technical Efficacy Thesaurus, Application Domain, Technology Topic, Popular Technical Reports.
© 2024 PatSnap. All rights reserved.Legal|Privacy policy|Modern Slavery Act Transparency Statement|Sitemap|About US| Contact US: help@patsnap.com