Control flow for manipulator of precision gear hobbing machine
A technology for controlling process and manipulators, which is applied to gear cutting machines, mechanical equipment, components with teeth, etc., can solve problems such as low production efficiency of automatic products, unstable system operation, and insufficient control process design of manipulators, etc., to achieve Improve the degree of automation and the effect of smooth operation
- Summary
- Abstract
- Description
- Claims
- Application Information
AI Technical Summary
Problems solved by technology
Method used
Image
Examples
Embodiment Construction
[0027] In order to make the technical means, creative features, goals and effects achieved by the present invention easy to understand, the present invention will be further elaborated below in conjunction with illustrations and specific embodiments.
[0028] refer to figure 1 As shown, the control process for the manipulator of the precision gear hobbing machine includes the manipulator taking out the workpiece from the tray, the manipulator returning the processed workpiece to the tray, and judging whether there is a workpiece on the tray. The steps are as follows :
[0029] S1, start the manipulator drive;
[0030] S2. The tray pushing mechanism pushes the tray into place;
[0031] S3, the manipulator takes out the workpieces from the tray in turn;
[0032] S4. Judging whether there are workpieces, if the workpieces on the tray are not finished, proceed to the next step S5;
[0033] S5. The feeding claw of the manipulator grabs the workpiece to be processed;
[0034] S...
PUM
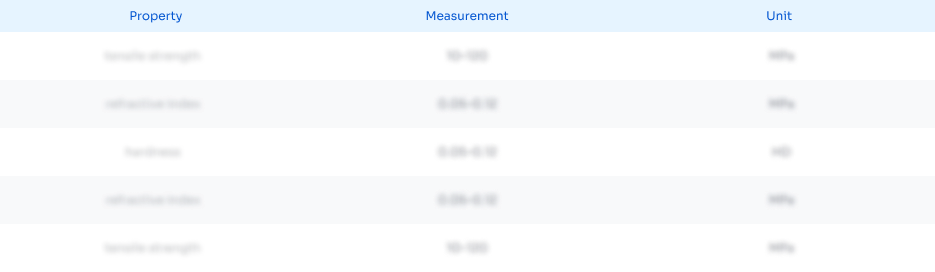
Abstract
Description
Claims
Application Information

- R&D Engineer
- R&D Manager
- IP Professional
- Industry Leading Data Capabilities
- Powerful AI technology
- Patent DNA Extraction
Browse by: Latest US Patents, China's latest patents, Technical Efficacy Thesaurus, Application Domain, Technology Topic, Popular Technical Reports.
© 2024 PatSnap. All rights reserved.Legal|Privacy policy|Modern Slavery Act Transparency Statement|Sitemap|About US| Contact US: help@patsnap.com