Wool fabric printing technology
A technology for fabric printing and wool, applied in animal fibers, textiles and papermaking, biochemical treatment of enzymes/microorganisms, etc. Felt shrinkage, bright color, avoid fabric yellowing effect
- Summary
- Abstract
- Description
- Claims
- Application Information
AI Technical Summary
Problems solved by technology
Method used
Examples
Embodiment 1
[0015] A wool fabric printing process, comprising the steps of:
[0016] (1) Composite enzyme chlorine-free anti-shrinkage pretreatment: soak the wool fabric in the compound enzyme chlorine-free anti-shrinkage finishing solution, padding for 28 minutes; wherein the compound enzyme chlorine-free anti-shrinkage finishing solution includes raw material components and their quality The percentages are: hydrogen peroxide 13%, potassium bisulfate 13%, compound enzyme 14%, silicone resin 2%, and the balance is water;
[0017] (2) Washing, dehydration and drying: wash the wool fabric after the compound enzyme chlorine-free anti-shrinkage pretreatment in step (1), and then dehydrate and dry;
[0018] (3) Printing: immerse the wool fabric treated in step (2) into the color paste, and then use a printing machine for printing treatment; wherein the raw material components and their mass percentages included in the color paste are: binder 13%, active 18% dye, 6% penetrant, and the rest is...
Embodiment 2
[0023] A wool fabric printing process, comprising the steps of:
[0024] (1) Composite enzyme chlorine-free anti-shrinkage pretreatment: soak the wool fabric in the compound enzyme chlorine-free anti-shrinkage finishing solution, padding for 38 minutes; wherein the compound enzyme chlorine-free anti-shrinkage finishing solution includes raw material components and their quality The percentages are: hydrogen peroxide 22%, potassium bisulfate 23%, compound enzyme 18%, silicone resin 8%, and the balance is water;
[0025] (2) Washing, dehydration and drying: wash the wool fabric after the compound enzyme chlorine-free anti-shrinkage pretreatment in step (1), and then dehydrate and dry;
[0026] (3) Printing: immerse the wool fabric treated in step (2) into the color paste, and then use a printing machine for printing treatment; wherein the raw material components and their mass percentages included in the color paste are: binder 15%, active 22% dye, 10% penetrant, and the rest i...
Embodiment 3
[0031] A wool fabric printing process, comprising the steps of:
[0032] (1) Composite enzyme chlorine-free anti-shrinkage pretreatment: soak the wool fabric in the compound enzyme chlorine-free anti-shrinkage finishing solution, padding for 33 minutes; wherein the compound enzyme chlorine-free anti-shrinkage finishing solution includes raw material components and their quality The percentages are: hydrogen peroxide 16%, potassium bisulfate 16%, compound enzyme 15%, silicone resin 5%, and the balance is water;
[0033] (2) Washing, dehydration and drying: wash the wool fabric after the compound enzyme chlorine-free anti-shrinkage pretreatment in step (1), and then dehydrate and dry;
[0034] (3) Printing: immerse the wool fabric treated in step (2) into the color paste, and then use a printing machine for printing treatment; wherein the color paste includes raw material components and their mass percentages: 14% binder, active 20% dye, 8% penetrant, and the rest is water;
...
PUM
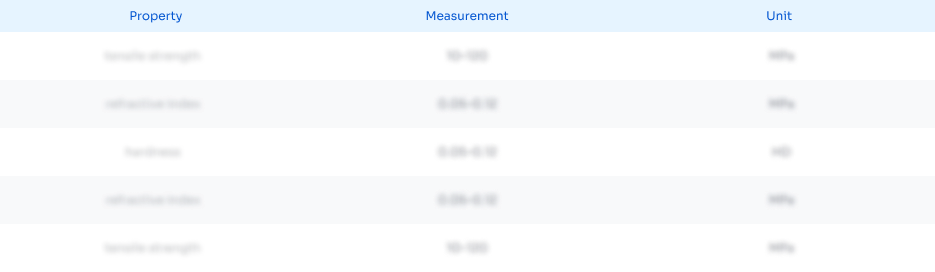
Abstract
Description
Claims
Application Information

- R&D Engineer
- R&D Manager
- IP Professional
- Industry Leading Data Capabilities
- Powerful AI technology
- Patent DNA Extraction
Browse by: Latest US Patents, China's latest patents, Technical Efficacy Thesaurus, Application Domain, Technology Topic, Popular Technical Reports.
© 2024 PatSnap. All rights reserved.Legal|Privacy policy|Modern Slavery Act Transparency Statement|Sitemap|About US| Contact US: help@patsnap.com