Automatic protection film removing mechanism
A protective film, automatic technology, used in printing machines, rotary printing machines, screen printing machines, etc., can solve the problems of high static electricity on the board, time-consuming and laborious, and contamination of the board, and achieves a clean surface of the board and high efficiency. , fast effect
- Summary
- Abstract
- Description
- Claims
- Application Information
AI Technical Summary
Problems solved by technology
Method used
Image
Examples
Embodiment Construction
[0013] figure 1 Shown is the schematic diagram of the use of the present invention, the plate is moved from the loading platform 1 to the suction conveying platform 2, the adhesive tape on the adhesive tape shaft 4 is pasted on the film on the surface of the plate and passed through the pressure roller 3 The bottom end moves forward, and the adhesive tape sticks to the film covering of the plate and then winds on the waste discharge shaft 5 to realize the automatic film removal of the plate.
[0014] Adjust the motor speed of the waste discharge shaft 5 so that the film removal speed of the board is synchronized with the conveying speed of the board, and adjust the magnetic brake at the rear end of the adhesive tape shaft 4 to stabilize the speed of the adhesive tape so that the adhesive tape rotates stably without slipping and the adhesive force it is good.
[0015] It can be seen that the automatic protective film removal mechanism automatically sticks the film on the board...
PUM
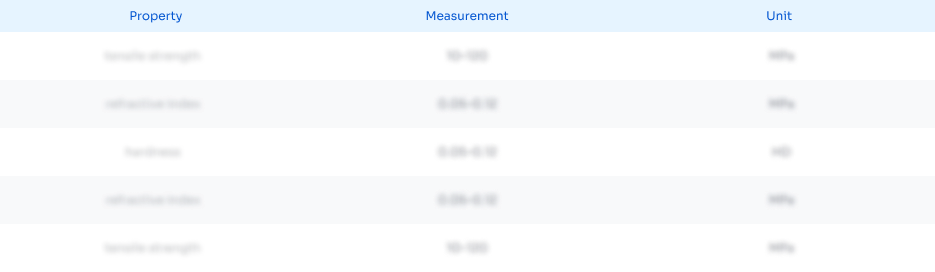
Abstract
Description
Claims
Application Information

- Generate Ideas
- Intellectual Property
- Life Sciences
- Materials
- Tech Scout
- Unparalleled Data Quality
- Higher Quality Content
- 60% Fewer Hallucinations
Browse by: Latest US Patents, China's latest patents, Technical Efficacy Thesaurus, Application Domain, Technology Topic, Popular Technical Reports.
© 2025 PatSnap. All rights reserved.Legal|Privacy policy|Modern Slavery Act Transparency Statement|Sitemap|About US| Contact US: help@patsnap.com