Washing agent for removing scale of cold-rolling acid-pickling regeneration set pipeline and using method thereof
A technology of cleaning agent and cold-rolled acid, which is applied in the field of water treatment, can solve problems such as incomplete cleaning, large potential safety hazards on site, and personal safety hazards of hydrofluoric acid, and achieves easy mastery of the preparation method and use method, and little harm to the human body , Excellent cleaning effect
- Summary
- Abstract
- Description
- Claims
- Application Information
AI Technical Summary
Problems solved by technology
Method used
Image
Examples
Embodiment 1
[0041] Prepare the cleaning agent as follows:
[0042] 1) Add 53 parts of ammonium bifluoride, 15 parts of sodium fluoride and 20 parts of 1 / 3 water into the melting tank A, mix and stir for 30 minutes to obtain the mixed solution a;
[0043] 2) Add 30 parts of trichlorethylene and 28 parts of diethyl ether into the melting tank B, mix and stir for 15 minutes to obtain the mixed solution b;
[0044] 3) Add 18 parts of polyvinylpyrrolidone K30 and 40 parts of 2 / 3 water into the melting tank C, stir for 30 minutes, then add 38 parts of nitric acid and 15 parts of acrylic acid-2-acrylamide-2-methylpropanesulfonic acid copolymer , continue mixing and stirring for 20 minutes to obtain a mixed solution c;
[0045] 4) Inject the above mixed solution a, mixed solution b and mixed solution c into the fusion pipeline at the same time, ensure that the fusion time is not less than 30 seconds, set the length of the fusion pipeline, and the mixed solution after fusion will be the cleaning ...
Embodiment 2
[0051] Prepare the cleaning agent as follows:
[0052] 1) Add 50 parts of ammonium bifluoride, 18 parts of sodium fluoride and 25 parts of 1 / 3 water into the melting tank A, mix and stir for 30 minutes to obtain the mixed solution a;
[0053] 2) Add 25 parts of trichlorethylene and 35 parts of diethyl ether into the melting tank B, mix and stir for 15 minutes to obtain the mixed solution b;
[0054] 3) Add 22 parts of polyvinylpyrrolidone K30 and 50 parts of 2 / 3 water into the melting tank C, stir for 30 minutes, then add 30 parts of nitric acid and 12 parts of acrylic acid-2-acrylamide-2-methylpropanesulfonic acid copolymer , continue mixing and stirring for 20 minutes to obtain a mixed solution c;
[0055] 4) Inject the above mixed solution a, mixed solution b and mixed solution c into the fusion pipeline at the same time, ensure that the fusion time is not less than 30 seconds, set the length of the fusion pipeline, and the mixed solution after fusion will be the cleaning ...
Embodiment 3
[0061] Prepare the cleaning agent as follows:
[0062] 1) Add 47 parts of ammonium bifluoride, 22 parts of sodium fluoride and 22 parts of 1 / 3 water into the melting tank A, mix and stir for 30 minutes to obtain the mixed solution a;
[0063] 2) Add 18 parts of trichlorethylene and 30 parts of diethyl ether into the melting tank B, mix and stir for 15 minutes to obtain the mixed solution b;
[0064] 3) Add 25 parts of polyvinylpyrrolidone K30 and 44 parts of 2 / 3 water into the melting tank C, stir for 30 minutes, then add 35 parts of nitric acid and 18 parts of acrylic acid-2-acrylamide-2-methylpropanesulfonic acid copolymer , continue mixing and stirring for 20 minutes to obtain a mixed solution c;
[0065] 4) Inject the above mixed solution a, mixed solution b and mixed solution c into the fusion pipeline at the same time, ensure that the fusion time is not less than 30 seconds, set the length of the fusion pipeline, and the mixed solution after fusion will be the cleaning ...
PUM
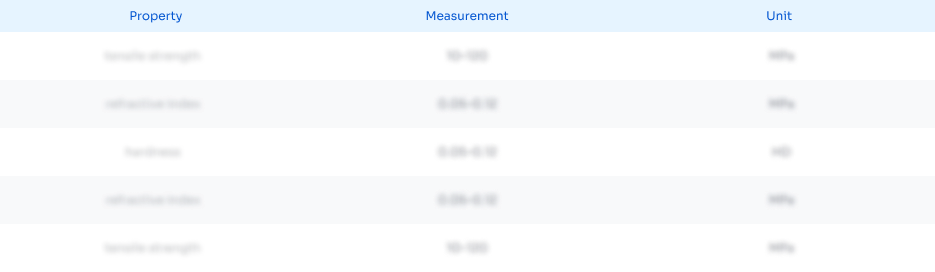
Abstract
Description
Claims
Application Information

- R&D
- Intellectual Property
- Life Sciences
- Materials
- Tech Scout
- Unparalleled Data Quality
- Higher Quality Content
- 60% Fewer Hallucinations
Browse by: Latest US Patents, China's latest patents, Technical Efficacy Thesaurus, Application Domain, Technology Topic, Popular Technical Reports.
© 2025 PatSnap. All rights reserved.Legal|Privacy policy|Modern Slavery Act Transparency Statement|Sitemap|About US| Contact US: help@patsnap.com