Antirust aluminum manganese welding wire production equipment
A production equipment and welding wire technology, which is applied in the field of anti-rust aluminum-manganese welding wire production equipment, can solve problems such as environmental hazards, improper acid treatment, and high production costs, and achieve the effects of improving production efficiency, improving production quality, and prolonging service life
- Summary
- Abstract
- Description
- Claims
- Application Information
AI Technical Summary
Problems solved by technology
Method used
Image
Examples
Embodiment 1
[0061] The following is attached Figure 1-12 The present invention is described in further detail.
[0062] A kind of antirust aluminum manganese welding wire production equipment, such as Figure 1-12 As shown, it includes a base 1, the upper part of the base 1 is fixedly equipped with a vertical plate 2, and the front side of the vertical plate 2 is sequentially installed with an unwinding roller 3, a correcting device 7, A sizing die 10, a tensioning device 8, and a winding roller 4 are fixedly installed through a rolling bearing. The top of the base 1 is positioned in front of the vertical plate 2, and a peeling roller is installed side by side through two lifting supports 9. Die 11 and polishing die 12, described peeling die 11 and described polishing die 12 are arranged between described sizing die 10 and described tensioning device 8, and described peeling die 11 is arranged on described polishing die 12 On the right side, one end of the winding roller 4 passes throu...
Embodiment 2
[0077] The difference from Example 1 is that preferably, the surface of the pulley 27 is also provided with a protective layer, and the protective layer is prepared by the following method:
[0078] Take the following raw materials and weigh them by weight: 20 parts of porcelain powder, 8 parts of titanium dioxide powder, 15 parts of aluminum oxide powder, 6 parts of talcum powder, 15 parts of epoxy resin, 13 parts of acrylic polyurethane, 2 parts of graphite powder, film-forming 4 parts of auxiliary agent, 2 parts of coupling agent, 3 parts of defoamer, 2 parts of leveling agent and 40 parts of methanol;
[0079] S1, adding porcelain powder, titanium dioxide powder, aluminum oxide powder, talc powder, epoxy resin, acrylic polyurethane and graphite powder into a ball mill for fine grinding to obtain a mixed powder material;
[0080] S2. Add the mixed powder material and methanol prepared in step S1 to the reaction kettle and stir for 20 min, then add film-forming aids, couplin...
Embodiment 3
[0087] The difference with embodiment 2 is the preparation of protective layer, and its specific preparation method is as follows:
[0088] Take the following raw materials and weigh them by weight: 25 parts of porcelain powder, 9 parts of titanium dioxide powder, 18 parts of aluminum oxide powder, 8 parts of talcum powder, 18 parts of epoxy resin, 15 parts of acrylic polyurethane, 4 parts of graphite powder, film-forming 5 parts of auxiliary agent, 3 parts of coupling agent, 4 parts of defoamer, 3 parts of leveling agent and 50 parts of methanol;
[0089] S1, adding porcelain powder, titanium dioxide powder, aluminum oxide powder, talc powder, epoxy resin, acrylic polyurethane and graphite powder into a ball mill for fine grinding to obtain a mixed powder material;
[0090] S2. Add the mixed powder material and methanol prepared in step S1 to the reaction kettle and stir for 25 min, then add film-forming aids, coupling agents, defoamers and leveling agents, and continue stirr...
PUM
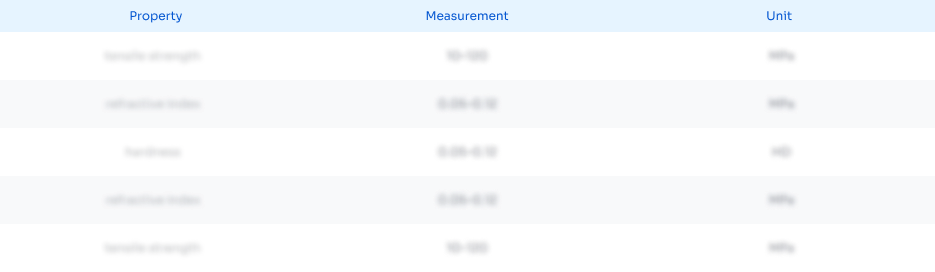
Abstract
Description
Claims
Application Information

- Generate Ideas
- Intellectual Property
- Life Sciences
- Materials
- Tech Scout
- Unparalleled Data Quality
- Higher Quality Content
- 60% Fewer Hallucinations
Browse by: Latest US Patents, China's latest patents, Technical Efficacy Thesaurus, Application Domain, Technology Topic, Popular Technical Reports.
© 2025 PatSnap. All rights reserved.Legal|Privacy policy|Modern Slavery Act Transparency Statement|Sitemap|About US| Contact US: help@patsnap.com