Variable stiffness joint of flexible robot
A robot and variable stiffness technology, applied in the direction of manipulators, manufacturing tools, joints, etc., can solve the problems of non-compactness, continuous adjustment of output stiffness, complex structure of variable stiffness joints, etc., to achieve constant stiffness, easy installation and maintenance, The effect of controlling simplification
- Summary
- Abstract
- Description
- Claims
- Application Information
AI Technical Summary
Problems solved by technology
Method used
Image
Examples
specific Embodiment approach 1
[0027] Specific implementation mode one: refer to figure 1 , the structure of the main motor module of the joint includes a main motor 1 , a main motor support 2 , a reducer 3 , and a main motor shaft sleeve 4 . The reducer 3 is a harmonic reducer with an ultra-flat hollow structure, small volume and large carrying capacity, which meets the requirements of actual operation. The shell of the main motor 1 is fixed on the main motor support 2, the output shaft of the main motor 1 is connected to the wave generator 5 of the harmonic reducer 3 through the main motor bushing 4, and the rigid wheel 6 of the harmonic reducer 3 is connected to the main motor The motor support 2 is fixed together by screws, and the flex spline of the harmonic reducer 3 is connected with the output disc 7 . The output shaft of the main motor 1 and the main motor shaft sleeve 4 are positioned circumferentially and axially through common flat keys and screws. This direct connection reduces the overall len...
specific Embodiment approach 2
[0029] Specific implementation mode two: combination figure 2 To illustrate, the middle cam roller module is a core module of a variable stiffness joint of a flexible robot, including a spline shaft 8, an upper cam disc 9, a middle disc 10, and a lower cam disc 11. The middle disc 10 has openings in the circumferential direction Six equal-diameter threaded holes, the spherical roller sleeve 14 is equipped with small deep groove ball bearings 13 to form a roller assembly, and the bolt shaft 12 fixes the six roller assemblies to the middle disc 10, and the sleeve I15 is used for radial position.
[0030] The middle disk 10 is connected with the spline shaft 8 through a spline, and the rotation of the spline shaft 8 drives the rotation of the middle disk 10, but the middle disk 10 can move along the axis of the spline shaft 8 due to the axial force. To slide, the spline acts as a guide. The upper cam disc 9 and the lower cam disc 11 are designed with the same curved surface sh...
specific Embodiment approach 3
[0032] Specific implementation mode three: combination image 3 Explain the relationship between the torque and stiffness of the variable stiffness joint and the passive rotation angle, image 3 It is the motion force analysis diagram of the intermediate cam roller module of the variable stiffness joint, which is drawn along the cam circumferential direction. The roller slides along the cam surface, the cam surface is generated by the curve, and the curve Γ is Y=f(θ) in the coordinate system θY-O, which can be further obtained:
[0033] Y B =f(θ B ), Y 3 =Y B +rcos(α B )
[0034] Y D =f(θ D ), Y 4 =Y D +rcos(α D )
[0035]
[0036] Ascent distance: Δy 1 =Y 3 -Y 1 , falling distance: Δy 2 =Y 4 -Y 2
[0037] The total compression of the spring: Δy=Δy 1 +Δy 2
[0038] Spring Force: F a = K spring *Δy
[0039] Upper cam disc torque: T 上凸轮盘 =F τ *R=F a Rtan(α D )
[0040] Lower cam disc torque: T 下凸轮盘 =F τ *R=F a Rtan(α B )
[0041] Joint o...
PUM
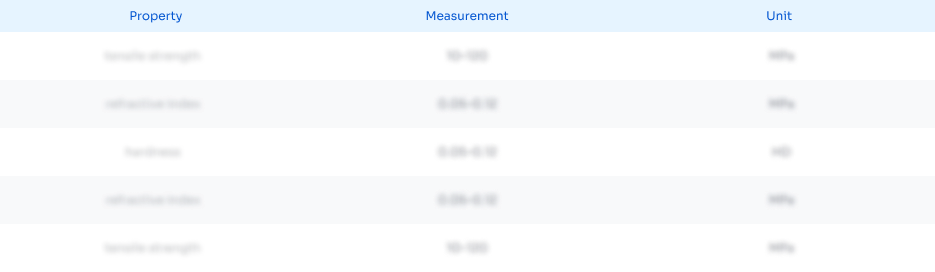
Abstract
Description
Claims
Application Information

- R&D
- Intellectual Property
- Life Sciences
- Materials
- Tech Scout
- Unparalleled Data Quality
- Higher Quality Content
- 60% Fewer Hallucinations
Browse by: Latest US Patents, China's latest patents, Technical Efficacy Thesaurus, Application Domain, Technology Topic, Popular Technical Reports.
© 2025 PatSnap. All rights reserved.Legal|Privacy policy|Modern Slavery Act Transparency Statement|Sitemap|About US| Contact US: help@patsnap.com