Method for recovering a lithium ion battery anode material
A lithium-ion battery and recycling method technology, applied in the field of waste lithium-ion battery treatment, can solve the problems of graphite raw material damage, graphitization difficulty, low reversible capacity, etc., to reduce graphitization temperature and time, and improve cycle stability , The effect of simple production process
- Summary
- Abstract
- Description
- Claims
- Application Information
AI Technical Summary
Problems solved by technology
Method used
Image
Examples
Embodiment 1
[0039] Collect the graphite slag left after the lithium-ion battery recovers metal, crush it and pass it through a 100-mesh sieve to obtain finer and more uniform graphite slag. Take 5kg of graphite slag, 0.5kg of asphalt, and 0.25kg of iron oxide powder, and mix them at a certain temperature. Under inert gas conditions, roast at 900°C for 5h; then transfer to a graphitization furnace, graphitize at 2000°C for 15h, ball mill and sieve, collect sieves with a particle size D50 of 15μm, and obtain a graphite negative electrode material.
Embodiment 2
[0041] Collect the graphite slag left after the lithium-ion battery recovers metal, crush it and pass it through a 100-mesh sieve to obtain finer and more uniform graphite slag. Take 5kg of graphite slag, 0.05kg of asphalt, and 0.5kg of iron oxide powder, and mix them at a certain temperature. Under inert gas conditions, roast at 1000°C for 6h; then transfer to a graphitization furnace, graphitize at 2000°C for 15h, ball mill and sieve, collect sieves with a particle size D50 of 15μm, and obtain graphite negative electrode materials.
Embodiment 3
[0043] Collect the graphite slag left after the lithium-ion battery recovers metal, crush it and pass through a 120-mesh sieve to obtain finer and more uniform graphite slag. Take 5kg of graphite slag with a particle size of less than 100 mesh, 1kg of asphalt, and 0.25kg of boron oxide powder, and mix them at a certain temperature. Under the condition of inert gas, it was roasted at 1100°C for 7h; then transferred to a graphitization furnace, graphitized at 2000°C for 10h, ball milled and sieved, and the sieve with particle size D50 of 15μm was collected to obtain graphite negative electrode material.
PUM
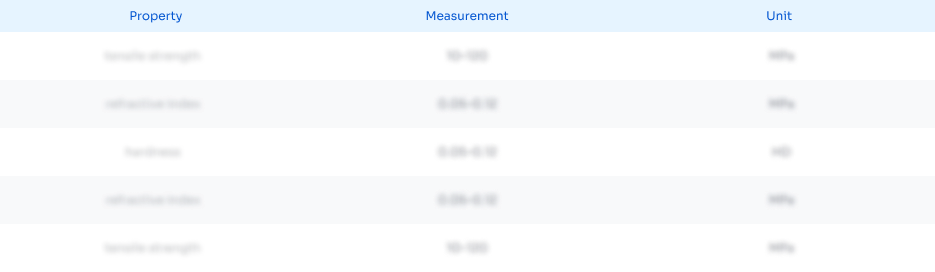
Abstract
Description
Claims
Application Information

- R&D Engineer
- R&D Manager
- IP Professional
- Industry Leading Data Capabilities
- Powerful AI technology
- Patent DNA Extraction
Browse by: Latest US Patents, China's latest patents, Technical Efficacy Thesaurus, Application Domain, Technology Topic, Popular Technical Reports.
© 2024 PatSnap. All rights reserved.Legal|Privacy policy|Modern Slavery Act Transparency Statement|Sitemap|About US| Contact US: help@patsnap.com