Method for preparing cyclopentanol or cyclopentanone by catalytically converting biomass
A technology for catalytic conversion and cyclopentanol, which is applied in the preparation of heterocyclic compounds, hydroxyl compounds, and organic compounds, etc., can solve problems such as increasing production costs, achieve reduced production costs, simple preparation methods, and good industrial application prospects. Effect
- Summary
- Abstract
- Description
- Claims
- Application Information
AI Technical Summary
Problems solved by technology
Method used
Image
Examples
Embodiment example 1
[0014] Weigh 0.9664g of copper nitrate trihydrate, 14.3590g of magnesium nitrate hexahydrate, and 7.503g of aluminum nitrate nonahydrate into a round bottom flask, and dissolve them in 400ml of deionized water as a solvent, which is designated as solution A. Weigh 10.5990g of sodium carbonate, 13.3333g of sodium hydroxide in a round bottom flask, and dissolve it in 400ml of deionized water as a solvent, which is designated as solution B. The solution A was slowly added to the solution B under stirring at room temperature, and the drop was completed in 2 hours. The mixed solution was circulated at 110° C. for 12 hours. Filter and wash to pH 7 with distilled water. Then vacuum-dried at 80°C in a vacuum oven for 12 hours, and the obtained precatalyst was calcined in a tube furnace under a nitrogen atmosphere to a temperature of 300°C with a heating rate of 5°C / min, and kept at this temperature for 4h. Then it was calcined in a tube furnace under a hydrogen atmosphere to a tempe...
Embodiment example 2
[0016] Weigh 1.9328g of copper nitrate trihydrate, 13.3333g of magnesium nitrate hexahydrate, and 7.503g of aluminum nitrate nonahydrate in a round bottom flask, and dissolve them in 400ml of deionized water as a solvent, which is recorded as solution A. Weigh 10.5990g of sodium carbonate, 13.3333g of sodium hydroxide in a round bottom flask, and dissolve it in 400ml of deionized water as a solvent, which is designated as solution B. The solution A was slowly added to the solution B under stirring at room temperature, and the drop was completed in 2 hours. The mixed solution was circulated at 110° C. for 12 hours. Filter and wash to pH 7 with distilled water. Then vacuum-dried at 80°C in a vacuum oven for 12 hours, and the obtained precatalyst was calcined in a tube furnace under a nitrogen atmosphere to a temperature of 300°C with a heating rate of 5°C / min, and kept at this temperature for 4h. Then it was calcined in a tube furnace under a hydrogen atmosphere to a temperatu...
Embodiment example 3
[0018] Weigh 2.8992g of copper nitrate trihydrate, 12.3077g of magnesium nitrate hexahydrate, and 7.503g of aluminum nitrate nonahydrate in a round-bottomed flask, and dissolve them in 400ml of deionized water as a solvent, which is recorded as solution A. Weigh 10.5990g of sodium carbonate, 13.3333g of sodium hydroxide in a round bottom flask, and dissolve it in 400ml of deionized water as a solvent, which is designated as solution B. The solution A was slowly added to the solution B under stirring at room temperature, and the drop was completed in 2 hours. The mixed solution was circulated at 110° C. for 12 hours. Filter and wash to pH 7 with distilled water. Then vacuum-dried in a vacuum oven at 80°C for 12 hours, and the obtained precatalyst was calcined in a tube furnace under a nitrogen atmosphere to a temperature of 300°C at a heating rate of 5°C / min, and kept at this temperature for 4 hours. Then it was calcined in a tube furnace under a hydrogen atmosphere to a temp...
PUM
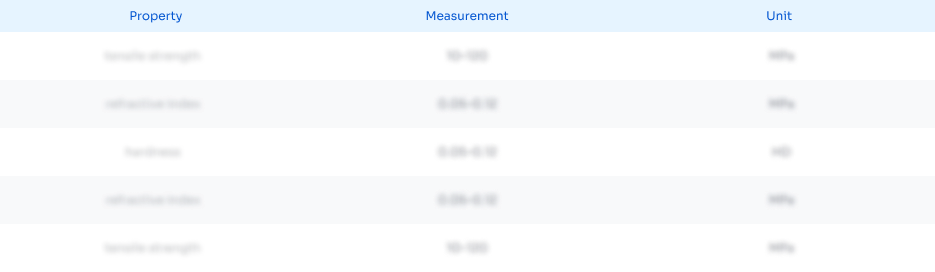
Abstract
Description
Claims
Application Information

- R&D
- Intellectual Property
- Life Sciences
- Materials
- Tech Scout
- Unparalleled Data Quality
- Higher Quality Content
- 60% Fewer Hallucinations
Browse by: Latest US Patents, China's latest patents, Technical Efficacy Thesaurus, Application Domain, Technology Topic, Popular Technical Reports.
© 2025 PatSnap. All rights reserved.Legal|Privacy policy|Modern Slavery Act Transparency Statement|Sitemap|About US| Contact US: help@patsnap.com