Armor plate and manufacturing method thereof
A production method and technology of bulletproof plate, applied in the direction of armor plate structure and other directions, can solve the problems of loose ceramics, affecting the ballistic resistance performance of the bulletproof plate, etc., and achieve the effect of enhancing the adhesion strength and improving the ballistic resistance performance.
- Summary
- Abstract
- Description
- Claims
- Application Information
AI Technical Summary
Problems solved by technology
Method used
Image
Examples
Embodiment 1
[0034] A polyethylene fiber layer with thermosetting adhesive attached thereon is provided, and multiple layers of polyethylene fiber are stacked from top to bottom. The thermosetting adhesive is a phenolic thermosetting adhesive.
[0035] Place a release film above and below the laminated multilayer polyethylene fibers, bond the surroundings of the release film with a sealant, feed the multilayer polyethylene fibers into a mold, and heat it to a set temperature. The set temperature is 132°C.
[0036] The multi-layer polyethylene fiber is laminated by four-stage lamination, wherein the curing pressure of the first stage is 6Mpa, the curing pressure of the second stage is 10Mpa, the curing pressure of the third stage is 16Mpa, and the curing pressure of the fourth stage is set to 16Mpa. The first stage of curing time is from room temperature to 90°C, the second stage of curing time is from 90°C to 128°C, the third stage of curing time is 3 hours of heat preservation and pressu...
Embodiment 2
[0039] A polyethylene fiber layer with thermosetting adhesive attached thereon is provided, and multiple layers of polyethylene fiber are stacked from top to bottom. The thermosetting adhesive is a phenolic thermosetting adhesive.
[0040] Place a release film above and below the laminated multilayer polyethylene fibers, bond the surroundings of the release film with a sealant, feed the multilayer polyethylene fibers into a mold, and heat it to a set temperature. The set temperature is 135°C.
[0041] The multi-layer polyethylene fiber is laminated by four-stage lamination, wherein the curing pressure of the first stage is 6Mpa, the curing pressure of the second stage is 10Mpa, the curing pressure of the third stage is 16Mpa, and the curing pressure of the fourth stage is set to 16Mpa. The first stage of curing time is from room temperature to 90°C, the second stage of curing time is from 90°C to 128°C, the third stage of curing time is 3 hours of heat preservation and pressu...
PUM
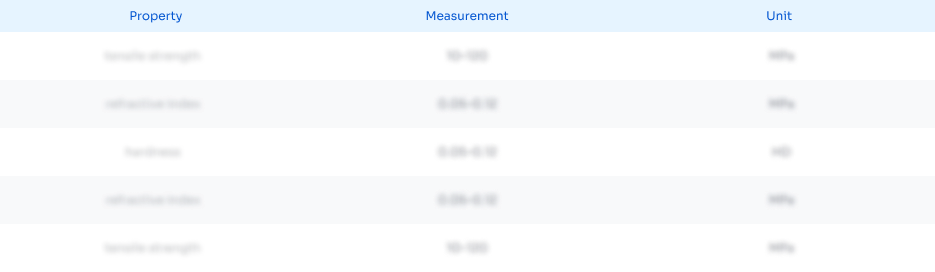
Abstract
Description
Claims
Application Information

- Generate Ideas
- Intellectual Property
- Life Sciences
- Materials
- Tech Scout
- Unparalleled Data Quality
- Higher Quality Content
- 60% Fewer Hallucinations
Browse by: Latest US Patents, China's latest patents, Technical Efficacy Thesaurus, Application Domain, Technology Topic, Popular Technical Reports.
© 2025 PatSnap. All rights reserved.Legal|Privacy policy|Modern Slavery Act Transparency Statement|Sitemap|About US| Contact US: help@patsnap.com