Precision machine tool dynamic performance optimization method based on frequency response calculation
A precision machine tool and dynamic performance technology, applied in the direction of design optimization/simulation, calculation, special data processing applications, etc., can solve the problems of inability to quantify, reduce, and the overall improvement level of dynamic performance is limited, so as to improve machining accuracy and realize dynamic characteristics , The effect of reducing the vibration level of the process
- Summary
- Abstract
- Description
- Claims
- Application Information
AI Technical Summary
Problems solved by technology
Method used
Image
Examples
Embodiment Construction
[0029] The working principle of the method of the present invention will be described in detail below with reference to the drawings and specific embodiments.
[0030] Such as figure 1 As shown, the precision machine tool dynamic performance optimization method of the frequency domain response calculation of the present invention, its steps are:
[0031] Step 1: Establish the model of the machine tool structural parts in the 3D design software, and properly simplify and correct the assembly model, and at the same time import it into the limited software for mesh division, and perform preprocessing on the definition of material properties, joint surfaces and boundary conditions, etc. ; The patented method can directly use the design model for processing, and the method is convenient and reliable.
[0032] Step 2: For different cutting processes, analyze the main causes of cutting dynamic force in the process, so as to establish a dynamic cutting force model in the frequency do...
PUM
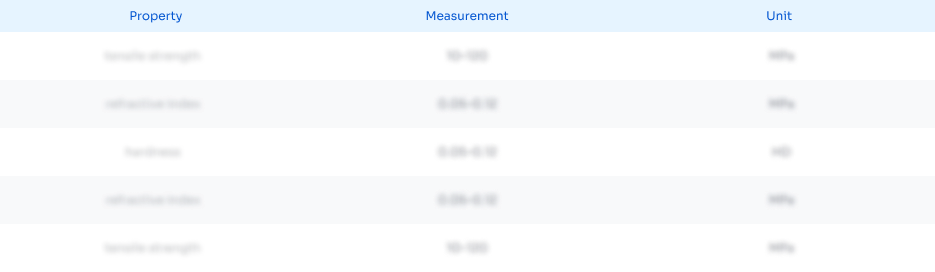
Abstract
Description
Claims
Application Information

- R&D Engineer
- R&D Manager
- IP Professional
- Industry Leading Data Capabilities
- Powerful AI technology
- Patent DNA Extraction
Browse by: Latest US Patents, China's latest patents, Technical Efficacy Thesaurus, Application Domain, Technology Topic, Popular Technical Reports.
© 2024 PatSnap. All rights reserved.Legal|Privacy policy|Modern Slavery Act Transparency Statement|Sitemap|About US| Contact US: help@patsnap.com