Preparation method of middle-low temperature coal tar hydrotreating catalyst Ni2P/SiO2 or Ni2P/Al2O3
A low-temperature coal tar and hydrotreating technology, which is applied in the direction of physical/chemical process catalysts, chemical instruments and methods, and petroleum industry, and can solve the problem of low preparation temperature
- Summary
- Abstract
- Description
- Claims
- Application Information
AI Technical Summary
Problems solved by technology
Method used
Image
Examples
Embodiment 1
[0018] 1. Prepare 0.86 moL / L nickel nitrate hexahydrate solution, and load nickel nitrate to SiO by equal volume impregnation 2 on the carrier.
[0019] 2. Dry the carrier at 80 °C for 12 h. The samples were then calcined at 330 °C in air for 5 h.
[0020] 3. Put 10 g of the calcined product into a tube furnace fed with hydrogen, and the hydrogen flow rate is 60 mL / min. Reduction was carried out at 350°C for 3 h.
[0021] 4. Transfer 4 g of the reduced product into a 1 L reactor and blow nitrogen into it. Weigh 0.105 g red phosphorus into the reactor (1.04 times the theoretical phosphorus consumption). The reactor was heated to 390 °C at a rate of 2 °C / min and then kept for 120 min. After the reaction, the reactor was cooled to room temperature. followed by 0.5 vol% O 2 / N 2 Mixed gas, the passivation time is 2 h, and the medium and low temperature coal tar hydrogenation catalyst with 27wt% Ni 2 P / SiO 2 .
Embodiment 2
[0023] 1. Prepare a 0.7 mol / L nickel acetate solution, and load nickel acetate onto SiO by equal volume impregnation 2 on the carrier.
[0024] 2. Dry the carrier at 100 °C for 10 h. The samples were then calcined at 350 °C for 5 h in air.
[0025] 3. Put 10 g of the calcined product into a tube furnace fed with hydrogen, and the hydrogen flow rate is 32 mL / min. Reduction was carried out at 360 °C for 6 h.
[0026] 4. Transfer 4 g of the reduced product into a 1 L reactor and blow nitrogen into it. Weigh 0.12 g red phosphorus into the reactor (1.06 times the theoretical phosphorus consumption). The reactor was heated to 400 °C at a rate of 3 °C / min and then kept for 100 min. After the reaction, the reactor was cooled to room temperature. followed by 0.5 vol% O 2 / N 2 , the passivation time is 3 h, and the medium and low temperature coal tar hydrogenation catalyst with 21 wt% Ni 2 P / SiO 2 .
Embodiment 3
[0028] 1. Prepare a 1 mol / L nickel acetate solution, and load nickel acetate onto SiO by equal volume impregnation 2 on the carrier.
[0029]2. Dry the carrier at 100 °C for 10 h. The samples were then calcined at 360 °C for 5 h in air.
[0030] 3. Put 10 g of the calcined product into a tube furnace fed with hydrogen, and the hydrogen flow rate is 45 mL / min. The reduction was carried out at 360°C, and the reduction time was 6 h.
[0031] 4. Transfer 4 g of the reduced product into a 1 L reactor and blow nitrogen into it. Weigh 0.13 g red phosphorus into the reactor (1.08 times the theoretical phosphorus consumption). The reaction kettle was heated to 404 °C at a rate of 3 °C / min and then kept for 100 min. After the reaction, the reactor was cooled to room temperature. followed by 0.5 vol% O 2 / N 2 , the passivation time is 4 h, and the medium and low temperature coal tar hydrogenation catalyst with 30wt% Ni 2 P / SiO 2 .
PUM
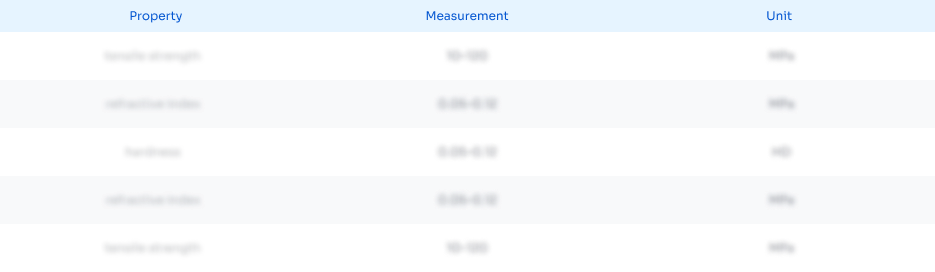
Abstract
Description
Claims
Application Information

- R&D
- Intellectual Property
- Life Sciences
- Materials
- Tech Scout
- Unparalleled Data Quality
- Higher Quality Content
- 60% Fewer Hallucinations
Browse by: Latest US Patents, China's latest patents, Technical Efficacy Thesaurus, Application Domain, Technology Topic, Popular Technical Reports.
© 2025 PatSnap. All rights reserved.Legal|Privacy policy|Modern Slavery Act Transparency Statement|Sitemap|About US| Contact US: help@patsnap.com