Precision multi-axis automatic wire stripping and tin dipping device and wire rod machining method
An automatic wire stripping and wire rod technology, applied in metal material coating process, hot-dip plating process, coating, etc., can solve the problems of low tin dipping efficiency, poor wire processing effect, and low control precision, so as to reduce manual labor Strength, increased productivity, and reduced overall volume
- Summary
- Abstract
- Description
- Claims
- Application Information
AI Technical Summary
Problems solved by technology
Method used
Image
Examples
Embodiment Construction
[0038] The following descriptions are only preferred embodiments of the present invention, and therefore do not limit the protection scope of the present invention.
[0039] Examples, see attached Figure 1 to Figure 8 , a precision multi-axis automatic stripping and tinning device 1 includes a wire processing device 2 and a multi-axis moving device 3, a tin-dipping driving mechanism 4 is provided between the wire processing device 2 and the multi-axis moving device 3, and the wire The processing device 2 includes a transmission mechanism 20, a thread cutting mechanism 21 and a wire core twisting mechanism 22, and the multi-axis moving device 3 includes a first moving mechanism 30, a second moving mechanism 31 and a turning mechanism 32, and the turning mechanism 32 is arranged on Between the first moving mechanism 30 and the second moving mechanism 31, the turning mechanism 32 is provided with a plurality of wire feeding assemblies 5;
[0040] Described first moving mechanis...
PUM
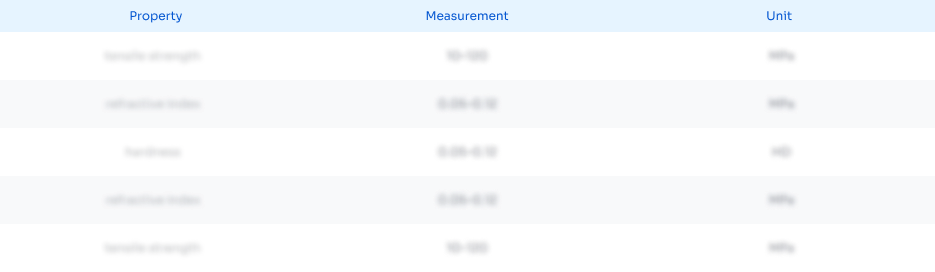
Abstract
Description
Claims
Application Information

- R&D
- Intellectual Property
- Life Sciences
- Materials
- Tech Scout
- Unparalleled Data Quality
- Higher Quality Content
- 60% Fewer Hallucinations
Browse by: Latest US Patents, China's latest patents, Technical Efficacy Thesaurus, Application Domain, Technology Topic, Popular Technical Reports.
© 2025 PatSnap. All rights reserved.Legal|Privacy policy|Modern Slavery Act Transparency Statement|Sitemap|About US| Contact US: help@patsnap.com