Method of preparing ammonium dimolybdate from a molybdenum-containing solution
A technology of ammonium dimolybdate and solution, applied in the field of separation chemistry, can solve the problems of high cost, low recovery rate, poor adaptability of raw materials, etc., and achieve the effect of low cost, short process and high recovery rate
- Summary
- Abstract
- Description
- Claims
- Application Information
AI Technical Summary
Problems solved by technology
Method used
Examples
Embodiment 1
[0047] A method for preparing ammonium dimolybdate from molybdenum-containing solution, comprising the following steps:
[0048] (1) Normal temperature vulcanization process:
[0049] Stir the molybdenum-containing solution, add ammonium sulfide at the same time, adjust the color of the solution from blue to colorless, let it stand for 24 hours, then pass the supernatant through a cardboard filter, and the filtrate is used as the raw material for the next acid precipitation process;
[0050] (2) Acid precipitation process:
[0051] Use anchor paddles to stir the filtrate obtained in the previous process, add industrial concentrated sulfuric acid, adjust the pH value of the filtrate to 2.8, stir for 30 minutes, pass through the ion exchange column for adsorption, and rinse the filter residue with pure water to obtain crude tetramolybdic acid Ammonium;
[0052] In the process of adding industrial concentrated sulfuric acid, the adding speed should be controlled to control the ...
PUM
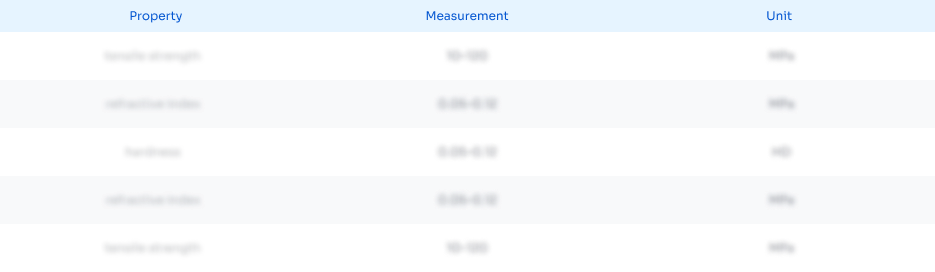
Abstract
Description
Claims
Application Information

- R&D Engineer
- R&D Manager
- IP Professional
- Industry Leading Data Capabilities
- Powerful AI technology
- Patent DNA Extraction
Browse by: Latest US Patents, China's latest patents, Technical Efficacy Thesaurus, Application Domain, Technology Topic, Popular Technical Reports.
© 2024 PatSnap. All rights reserved.Legal|Privacy policy|Modern Slavery Act Transparency Statement|Sitemap|About US| Contact US: help@patsnap.com