Electrostatic self-assembling preparation method of graphene/silicon electrode material
A technology of electrostatic self-assembly and graphene, which is applied in nanotechnology for materials and surface science, negative electrodes, battery electrodes, etc., can solve the problems of silicon/graphene composite electrode materials that need to be improved, limited performance, and high cost. Achieve the effect of being suitable for large-scale production and application, suppressing volume effect, and blocking direct contact
- Summary
- Abstract
- Description
- Claims
- Application Information
AI Technical Summary
Problems solved by technology
Method used
Image
Examples
Embodiment 1
[0023] (1) Mix 60g of iodine bromide and 100mg of expanded graphite evenly, vacuum seal it in a 50mL airtight glass bottle, place it in an oil bath environment at 100°C, and heat for 12h to prepare a graphite intercalation compound. The graphite intercalation compound is quickly removed from the Remove from a glass bottle and filter.
[0024] (2) Put the intercalation compound into a hydrothermal kettle with a volume of 50 mL quickly, heat the temperature to 220° C., and keep it for 1 hour. The interlayer reaction generates gas and exfoliates to obtain a graphene material.
[0025] (3) 100 mg of graphene and 200 mg of potassium permanganate were added to 100 mL of concentrated sulfuric acid, and treated in an ice-bath environment for 4 hours to obtain graphene oxide.
[0026] (4) Hydrofluoric acid was used to etch the oxide on the surface of the silicon particles. After etching for 10 minutes, the product obtained was cleaned with absolute ethanol, and then the etched nano-sil...
Embodiment 2
[0035] (1) Mix 60g of iodine bromide and 100mg of expanded graphite evenly, vacuum seal it in a 50mL airtight glass bottle, place it in an oil bath environment at 100°C, and heat for 12h to prepare a graphite intercalation compound. The graphite intercalation compound is quickly removed from the Remove from a glass bottle and filter.
[0036] (2) Put the intercalation compound into a hydrothermal kettle with a volume of 50 mL quickly, heat the temperature to 220° C., and keep it for 1 hour. The interlayer reaction generates gas and exfoliates to obtain a graphene material.
[0037] (3) 100 mg of graphene and 400 mg of potassium permanganate were added to 100 mL of concentrated sulfuric acid, and treated in an ice-bath environment for 4 hours to obtain graphene oxide.
[0038] (4) Hydrofluoric acid was used to etch the oxide on the surface of the silicon particles. After etching for 10 minutes, the product obtained was cleaned with absolute ethanol, and then the etched nano-sil...
Embodiment 3
[0044] (1) Mix 60g of iodine bromide and 100mg of expanded graphite evenly, vacuum seal it in a 50mL airtight glass bottle, place it in an oil bath environment at 100°C, and heat for 12h to prepare a graphite intercalation compound. The graphite intercalation compound is quickly removed from the Remove from a glass bottle and filter.
[0045] (2) Put the intercalation compound into a hydrothermal kettle with a volume of 50 mL quickly, heat the temperature to 220° C., and keep it for 1 hour. The interlayer reaction generates gas and exfoliates to obtain a graphene material.
[0046] (3) 100 mg of graphene and 400 mg of potassium permanganate were added to 100 mL of concentrated sulfuric acid, and treated in an ice-bath environment for 1 h to obtain graphene oxide.
[0047] (4) Hydrofluoric acid was used to etch the oxide on the surface of the silicon particles. After etching for 10 minutes, the product obtained was cleaned with absolute ethanol, and then the etched nano-silicon p...
PUM
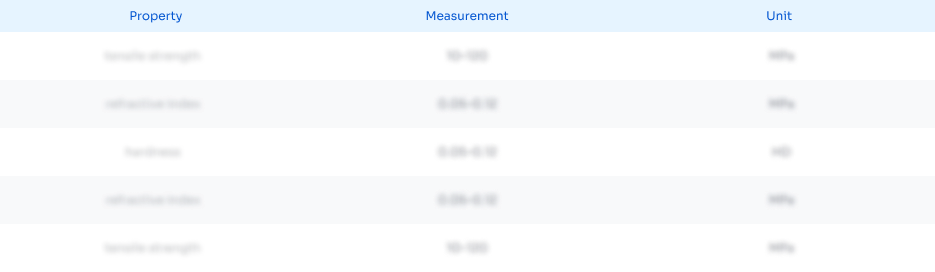
Abstract
Description
Claims
Application Information

- R&D
- Intellectual Property
- Life Sciences
- Materials
- Tech Scout
- Unparalleled Data Quality
- Higher Quality Content
- 60% Fewer Hallucinations
Browse by: Latest US Patents, China's latest patents, Technical Efficacy Thesaurus, Application Domain, Technology Topic, Popular Technical Reports.
© 2025 PatSnap. All rights reserved.Legal|Privacy policy|Modern Slavery Act Transparency Statement|Sitemap|About US| Contact US: help@patsnap.com