Machining method for shower-type injector adopting thin guide pipes
A processing method and injector technology, which are applied in the field of liquid rocket engine preparation, can solve the problems of high requirements on end face geometry, inconsistent height of thin conduits, insufficient welding seam strength, etc., so as to reduce the processing requirements of fine holes and avoid brazing filler metals. Floating, high-efficiency effects
- Summary
- Abstract
- Description
- Claims
- Application Information
AI Technical Summary
Problems solved by technology
Method used
Image
Examples
Embodiment Construction
[0027] The present invention will be further described in detail below in conjunction with the accompanying drawings to facilitate a clearer understanding of the present invention, but they do not limit the present invention.
[0028] A method for processing a showerhead injector using a thin conduit, comprising the following steps:
[0029] 1) Parts of the machine injector, such as figure 1 As shown, the injector includes an upper injection plate 1 , a lower injection plate 3 , a squirrel cage 2 and a thin conduit 4 . The upper injection plate 1 is made of high-temperature alloy 3536, and several through holes with a diameter of 0.7mm are machined on the upper injection plate 1, that is, the upper connection hole 1.1 of the thin conduit is ensured to be 0.03 to 0.8 larger than the outer diameter of the thin conduit 4. mm, and add C0.5~C1 chamfer 7 to the through hole with chamfered non-injection surface 10, that is, add chamfer 7 to the lower end of the upper connection hole...
PUM
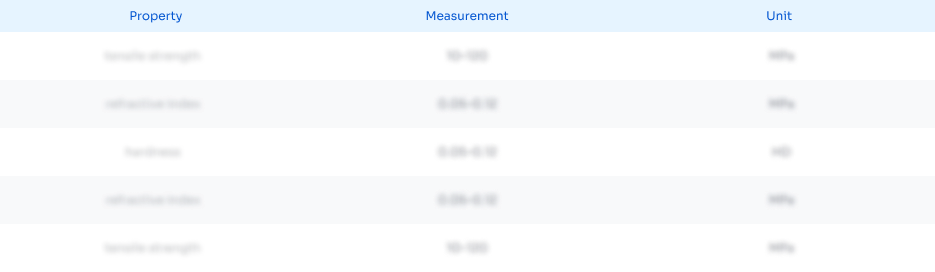
Abstract
Description
Claims
Application Information

- Generate Ideas
- Intellectual Property
- Life Sciences
- Materials
- Tech Scout
- Unparalleled Data Quality
- Higher Quality Content
- 60% Fewer Hallucinations
Browse by: Latest US Patents, China's latest patents, Technical Efficacy Thesaurus, Application Domain, Technology Topic, Popular Technical Reports.
© 2025 PatSnap. All rights reserved.Legal|Privacy policy|Modern Slavery Act Transparency Statement|Sitemap|About US| Contact US: help@patsnap.com