Wood floor wax
A wood floor and paraffin wax technology, applied in the field of wood floor wax, can solve problems such as insufficient wear resistance and easy scratching, and achieve the effects of increasing service life, improving internal bonding force, and improving service life
- Summary
- Abstract
- Description
- Claims
- Application Information
AI Technical Summary
Problems solved by technology
Method used
Examples
example 1
[0027]Mix aluminum chloride and water at a mass ratio of 1:8, adjust the pH of the mixture of aluminum chloride and water to 4.1 with ammonia water, stir and mix for 30 minutes at a temperature of 50°C and a speed of 350r / min to obtain alumina Sol, mix alumina sol and sodium dodecylbenzenesulfonate in a flask at a mass ratio of 10:3, and add xylene that is 1.0 times the mass of alumina sol to the flask, and let stand at room temperature to separate layers. Remove the lower layer liquid to obtain a pretreated organosol, distill the pretreated organosol under reduced pressure to remove excess xylene to obtain an organosol, and calcinate the organosol at a temperature of 800°C for 2 hours to obtain modified alumina; Mix Acetobacter xylinum and culture solution in a petri dish at a mass ratio of 1:150, and add modified alumina 0.15 times the mass of the culture solution to the petri dish, at a temperature of 40°C and a rotation speed of 300r / min. After stirring and mixing for 20 m...
example 2
[0029] Mix Acetobacter xylinum and culture solution in a petri dish at a mass ratio of 1:150, and add aluminum oxide 0.15 times the mass of the culture solution to the petri dish, and stir and mix at a temperature of 40°C and a speed of 300r / min. After 20 minutes, cultivate at a constant temperature of 35°C for 8 days, filter to obtain a filter cake, wash the filter cake with water for 4 times, freeze-dry and pulverize to obtain pretreated bacterial cellulose; mix ethyl orthosilicate with Water is mixed in the conical flask at a mass ratio of 1:5, and 0.3 times the mass fraction of ethyl orthosilicate is added to the conical flask, and 20% of the pretreated bacterial cellulose is ammonia water and 0.8 times the ethyl orthosilicate. , stirred and mixed for 50 minutes at a temperature of 50°C and a rotational speed of 300r / min, then stood still at a temperature of 40°C for 2 hours, filtered to obtain a filter residue, and dried the filter residue at a temperature of 80°C for 40 m...
example 3
[0031] Mix Acetobacter xylinum and culture solution in a petri dish at a mass ratio of 1:150, stir and mix for 20 minutes at a temperature of 40°C and a rotation speed of 300r / min, and then culture at a constant temperature of 35°C for 8 days , filter to obtain filter cake, wash the filter cake with water for 4 times, freeze-dry and pulverize to obtain bacterial cellulose; mix ethyl orthosilicate and water in a conical flask at a mass ratio of 1:5, and pour Add 0.3 times the mass fraction of ethyl orthosilicate to the shaped bottle, 20% ammonia water and 0.8 times the pretreated bacterial cellulose of ethyl orthosilicate, stir and mix at a temperature of 50°C and a rotation speed of 300r / min After 50 minutes, after standing at a temperature of 40° C. for 2 hours, filter to obtain a filter residue, and dry the filter residue at a temperature of 80° C. for 40 minutes to obtain pre-modified bacterial cellulose. The pre-modified bacterial cellulose Mix it with water in a beaker at...
PUM
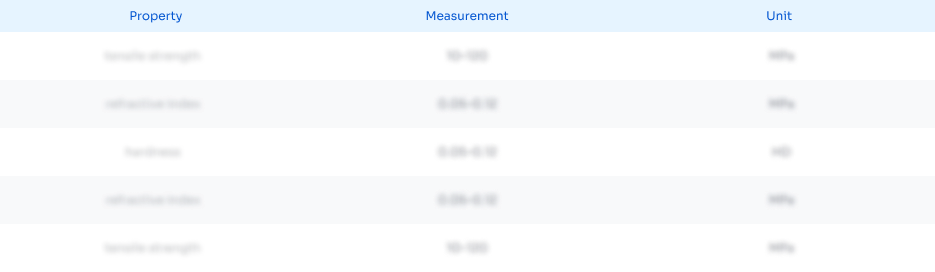
Abstract
Description
Claims
Application Information

- Generate Ideas
- Intellectual Property
- Life Sciences
- Materials
- Tech Scout
- Unparalleled Data Quality
- Higher Quality Content
- 60% Fewer Hallucinations
Browse by: Latest US Patents, China's latest patents, Technical Efficacy Thesaurus, Application Domain, Technology Topic, Popular Technical Reports.
© 2025 PatSnap. All rights reserved.Legal|Privacy policy|Modern Slavery Act Transparency Statement|Sitemap|About US| Contact US: help@patsnap.com