Fiber reinforced thermal insulation concrete wall body
A thermal insulation concrete and fiber reinforced technology, applied in the field of fiber reinforced thermal insulation concrete walls, can solve problems such as damage and micro-cracks
- Summary
- Abstract
- Description
- Claims
- Application Information
AI Technical Summary
Problems solved by technology
Method used
Image
Examples
preparation example Construction
[0019] The present invention also provides a method for preparing the fiber-reinforced thermal insulation concrete wall, comprising the following steps:
[0020] (1) Spinning after mixing the first polymer emulsion and the second blowing agent uniformly to obtain polymer fibers; then placing the polymer fibers, chain extenders and metal oxide powders in the second polymer emulsion, React at 60-100°C for 15-60 minutes, then soak in acidic solution to obtain composite porous fibers;
[0021] (2) Mix fly ash, cement, fine sand, diatomaceous earth, light calcium carbonate, light aggregate, composite porous fiber and waste rubber under mechanical stirring conditions to obtain a powder mixture;
[0022] (3) After uniformly dispersing the water reducer and other additives in water, add them to the above powder mixture, and continue to stir for 60-150s to obtain a mixed slurry; finally, add the first foaming agent to the mixed slurry, and stir evenly to obtain Concrete precursor;
...
Embodiment 1
[0029] (1) Spin after mixing 24kg polyethylene terephthalate emulsion and 6kg 4,4-oxobisbenzenesulfonyl hydrazide evenly to obtain polyethylene terephthalate fibers, and the spinning process is: The power supply voltage is 30kV, the spinning temperature is 25°C, and the relative humidity is 60%; the needle spacing of the multi-needle spinneret unit is 25cm, and the number of spinneret unit needleheads is 60; 22kg polyethylene terephthalate fiber, 20kg ethylene glycol and Put 1.2kg of zinc nitrate in 12kg of polyethylene terephthalate emulsion, react at 80°C for 45 minutes to obtain polymer fibers, then soak the polymer fibers in a hydrochloric acid solution with a pH of 3 for 2 hours, and replace them every 15 minutes A hydrochloric acid solution to obtain a composite porous fiber;
[0030] Soak 4kg of waste rubber granules in an acidic solution with a pH of 6-6.5 for 4 hours to obtain acidified rubber, mix the acidified rubber and 10kg of maleic anhydride in water evenly, and...
Embodiment 2
[0035] (1) 20kg of nylon 6 emulsion and 2kg of 4,4-oxobisbenzenesulfonyl hydrazide are mixed evenly and then spun to obtain nylon 6 fiber. The spinning process is: power supply voltage 30kV, spinning temperature 25°C, relative The humidity is 60%; the distance between the needles of the multi-needle spinning unit is 25cm, and the number of needles in the spinning unit is 60; 18kg of nylon 6 fibers, 24kg of 1,3-butanediol and 2kg of zinc oxide are placed in 10kg of nylon 6 emulsion, at 80°C React at low temperature for 30 minutes to obtain polymer fibers, then soak the polymer fibers in a hydrochloric acid solution with a pH of 2 for 1.5 hours, wherein the hydrochloric acid solution is replaced every 15 minutes to obtain composite fibers B, and treat composite fibers B at 150°C for 30 minutes, composite porous fiber
[0036] Soak 3kg of waste rubber particles in an acidic solution with a pH of 6-6.5 for 3 hours to obtain acidified rubber, mix the acidified rubber and 9kg of mal...
PUM
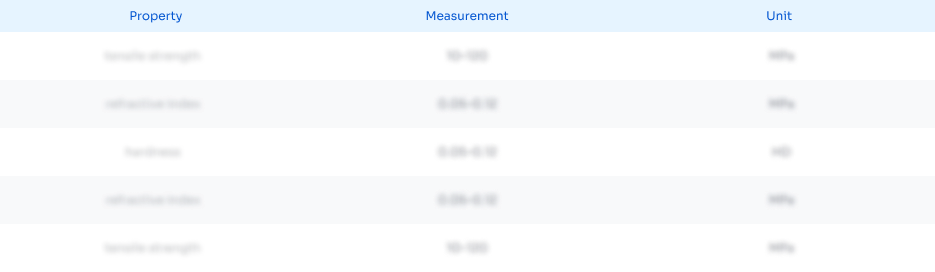
Abstract
Description
Claims
Application Information

- R&D
- Intellectual Property
- Life Sciences
- Materials
- Tech Scout
- Unparalleled Data Quality
- Higher Quality Content
- 60% Fewer Hallucinations
Browse by: Latest US Patents, China's latest patents, Technical Efficacy Thesaurus, Application Domain, Technology Topic, Popular Technical Reports.
© 2025 PatSnap. All rights reserved.Legal|Privacy policy|Modern Slavery Act Transparency Statement|Sitemap|About US| Contact US: help@patsnap.com