Combined special-shaped cast pipe and production method thereof
A combined casting pipe technology, which is applied to casting molding equipment, cores, casting molds, etc., can solve the problems of poor surface roughness, high comprehensive price, and low precision, and achieve smooth surface, convenient construction, and beautiful pipes Effect
- Summary
- Abstract
- Description
- Claims
- Application Information
AI Technical Summary
Problems solved by technology
Method used
Image
Examples
Embodiment 1
[0021] Such as figure 1 As shown, a combined special-shaped casting pipe in this embodiment is composed of an adhesive 1, an adhesive 3 and a straight pipe 5. The adhesive 1 is cast by sand casting, and its adhesive fit Surface 2 is processed by machining to meet the requirements of bonding accuracy and smoothness; straight pipe 5 is made by centrifugal casting, and its bonding surface 4 is processed by machining to meet the requirements of bonding accuracy and smoothness. The joint surface 4 and the adhesive mating surface 2 of the adhesive member 1 are bonded with an adhesive 3 so that the straight pipe 5 and the adhesive member 1 are integrated.
[0022] The outer diameter of the adhesive mating surface 2 of the adhesive member 1 is 0.5-1mm smaller than the inner diameter of the adhesive surface 4 of the straight pipe 5, and the taper of the adhesive mating surface 2 of the adhesive member 1 is 3°. The taper of the bonding surface 4 of the straight pipe 5 is the same as th...
Embodiment 2
[0032] Such as figure 1 As shown, a combined special-shaped casting pipe in this embodiment is composed of an adhesive 1, an adhesive 3 and a straight pipe 5. The adhesive 1 is cast by sand casting, and its adhesive fit Surface 2 is processed by machining to meet the requirements of bonding accuracy and smoothness; straight pipe 5 is made by centrifugal casting, and its bonding surface 4 is processed by machining to meet the requirements of bonding accuracy and smoothness. The joint surface 4 and the adhesive mating surface 2 of the adhesive member 1 are bonded with an adhesive 3 so that the straight pipe 5 and the adhesive member 1 are integrated.
[0033] The outer diameter of the adhesive mating surface 2 of the adhesive member 1 is 0.5-1mm smaller than the inner diameter of the adhesive surface 4 of the straight pipe 5, and the taper of the adhesive mating surface 2 of the adhesive member 1 is 3°. The taper of the bonding surface 4 of the straight pipe 5 is the same as th...
Embodiment 3
[0043] Such as figure 1 As shown, a combined special-shaped casting pipe in this embodiment is composed of an adhesive 1, an adhesive 3 and a straight pipe 5. The adhesive 1 is cast by sand casting, and its adhesive fit Surface 2 is processed by machining to meet the requirements of bonding accuracy and smoothness; straight pipe 5 is made by centrifugal casting, and its bonding surface 4 is processed by machining to meet the requirements of bonding accuracy and smoothness. The joint surface 4 and the adhesive mating surface 2 of the adhesive member 1 are bonded with an adhesive 3 so that the straight pipe 5 and the adhesive member 1 are integrated.
[0044] The outer diameter of the adhesive mating surface 2 of the adhesive member 1 is 0.5-1mm smaller than the inner diameter of the adhesive surface 4 of the straight pipe 5, and the taper of the adhesive mating surface 2 of the adhesive member 1 is 3°. The taper of the bonding surface 4 of the straight pipe 5 is the same as th...
PUM
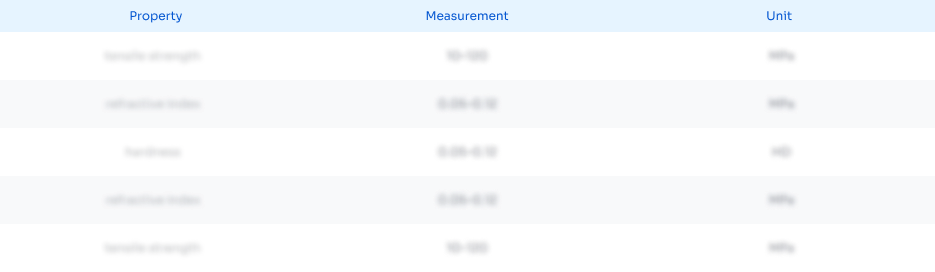
Abstract
Description
Claims
Application Information

- R&D
- Intellectual Property
- Life Sciences
- Materials
- Tech Scout
- Unparalleled Data Quality
- Higher Quality Content
- 60% Fewer Hallucinations
Browse by: Latest US Patents, China's latest patents, Technical Efficacy Thesaurus, Application Domain, Technology Topic, Popular Technical Reports.
© 2025 PatSnap. All rights reserved.Legal|Privacy policy|Modern Slavery Act Transparency Statement|Sitemap|About US| Contact US: help@patsnap.com