Ball-end mill for milling curved surface splicing molds
A ball-end milling cutter and splicing mold technology, applied in milling cutters, manufacturing tools, milling machine equipment, etc., can solve the problems of poor surface quality and high processing cost of processed workpieces, increase contact area, improve processing quality, and improve processing The effect of precision
- Summary
- Abstract
- Description
- Claims
- Application Information
AI Technical Summary
Problems solved by technology
Method used
Image
Examples
specific Embodiment approach 1
[0023] Specific implementation mode one: as Figure 1~3 As shown, the profile of the ball-end milling cutter for splicing mold milling in this embodiment is in the shape of a round cake, and two cutting edges are processed on the ball-end milling cutter, and the two cutting edges are the first cutting edge 1 and the second cutting edge respectively. Two cutting edges 4, the first cutting edge 1 and the second cutting edge 4 are sinusoidal cutting edges, one side of the first cutting edge 1 is connected with the first rake face 2, and the first rake face 2 is lower than the ball head The upper surface 7 of the milling cutter is set and the two are arranged in parallel, the first rake surface 2 and the upper surface 7 of the ball end milling cutter are transitionally connected through the first groove surface 3, and the other side of the first cutting edge 1 is connected with the first rear Cutter face 9; one side of the second cutting edge 4 is connected with a second rake face...
specific Embodiment approach 2
[0024] Specific implementation mode two: as Figure 1~3 As shown, the first groove surface 3 and the second groove surface 12 in this embodiment are both concave curved surfaces. Such a design increases the contact area between the tool holder and the blade, making it difficult for the blade to loosen during the milling process, thereby improving the machining accuracy of the parts. Other components and connections are the same as those in the first embodiment.
specific Embodiment approach 3
[0025] Specific implementation mode three: as image 3 with Figure 4 As shown, the edge A of the first cutting edge 1 in this embodiment is a composite structure of chamfers 16 and blunt circles 15 . Designed in this way, the structure greatly improves the impact resistance of the cutting edge, reduces the wear rate of the first flank face at the same time, and improves the service life of the tool and the surface processing quality of the workpiece. Other compositions and connections are the same as those in Embodiment 1 or 2.
PUM
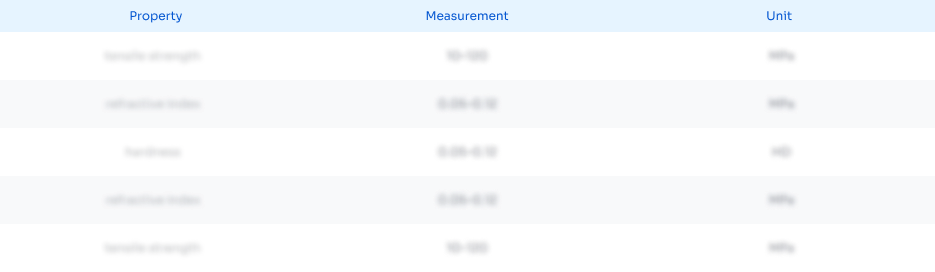
Abstract
Description
Claims
Application Information

- R&D Engineer
- R&D Manager
- IP Professional
- Industry Leading Data Capabilities
- Powerful AI technology
- Patent DNA Extraction
Browse by: Latest US Patents, China's latest patents, Technical Efficacy Thesaurus, Application Domain, Technology Topic, Popular Technical Reports.
© 2024 PatSnap. All rights reserved.Legal|Privacy policy|Modern Slavery Act Transparency Statement|Sitemap|About US| Contact US: help@patsnap.com