Zinc oxide composite photocatalyst, preparation method and application thereof
A technology of zinc oxide and composite light, which is applied in the chemical field, can solve the problems of small specific surface area, ZnO cannot provide active reaction sites, and affect the photocatalytic performance of ZnO crystals, and achieve large specific surface area, no secondary pollution, and photocatalytic The effect of high reactivity
- Summary
- Abstract
- Description
- Claims
- Application Information
AI Technical Summary
Problems solved by technology
Method used
Image
Examples
Embodiment 1
[0020] A zinc oxide-based composite catalytic preparation method for photocatalytically degrading formaldehyde, comprising the following steps:
[0021] 1. Preparation of 3D porous zinc oxide: Weigh 2.7g of zinc nitrate hexahydrate and dissolve it in 20mL of deionized water, add dropwise (1 drop / s) an aqueous solution containing 1.27g of hexamethylenetetramine and 0.3g of oxalic acid dihydrate 30mL, and magnetically stirred to make it fully dissolved, the mixed solution was condensed and refluxed in an oil bath at 80°C for 4 hours to obtain a white precipitate, which was washed with deionized water several times, and then placed in a vacuum oven (50°C ) is dried for 24 hours to form zinc oxide. The zinc oxide is placed in a muffle furnace and calcined at 500° C. for 3 hours in an air atmosphere to obtain a porous ZnO product.
[0022] 2. Preparation of Ag / ZnO composite material: Weigh 0.0559g of silver nitrate, dissolve it in 100mL of deionized water, then weigh 0.1342g of the...
Embodiment 2
[0025] 1. Preparation of 3D porous zinc oxide: Weigh 2.7g of zinc nitrate hexahydrate and dissolve it in 20mL of deionized water, add dropwise (1 drop / s) an aqueous solution containing 2.54g of hexamethylenetetramine and 0.3g of oxalic acid dihydrate 30mL, and magnetically stirred to make it fully dissolved, the mixed solution was condensed and refluxed in an oil bath at 80°C for 4 hours to obtain a white precipitate, which was washed with deionized water several times, and then placed in a vacuum oven (50°C ) is dried for 24 hours to form zinc oxide. The zinc oxide is placed in a muffle furnace and calcined at 400° C. for 4 hours in an air atmosphere to obtain a porous ZnO product.
[0026] 2. Preparation of Ag / ZnO composite material: Weigh 0.1399g of silver nitrate, dissolve it in 100mL of deionized water, then weigh 0.1342g of the 3D porous zinc oxide sample prepared in step 1, and add it to the silver nitrate solution , stir the mixed solution magnetically (300-500r / min) f...
Embodiment 3
[0029]1. Preparation of 3D porous zinc oxide: Weigh 2.7g of zinc nitrate hexahydrate and dissolve it in 20mL of deionized water, add dropwise (1 drop / s) an aqueous solution containing 1.27g of hexamethylenetetramine and 0.572g of oxalic acid dihydrate 30mL, and magnetically stirred to make it fully dissolved, the mixed solution was condensed and refluxed in an oil bath at 80°C for 4 hours to obtain a white precipitate, which was washed with deionized water several times, and then placed in a vacuum oven (50°C ) is dried for 24 hours to form zinc oxide. The zinc oxide is placed in a muffle furnace and calcined at 400° C. for 4 hours in an air atmosphere to obtain a porous ZnO product.
[0030] 2. Preparation of Ag / ZnO composite material: Weigh 0.0131g of silver nitrate, dissolve it in 100mL of deionized water, then weigh 0.1342g of the 3D porous zinc oxide sample prepared in step 1, and add it to the silver nitrate solution , magnetically stir the mixed solution (300-500r / min) ...
PUM
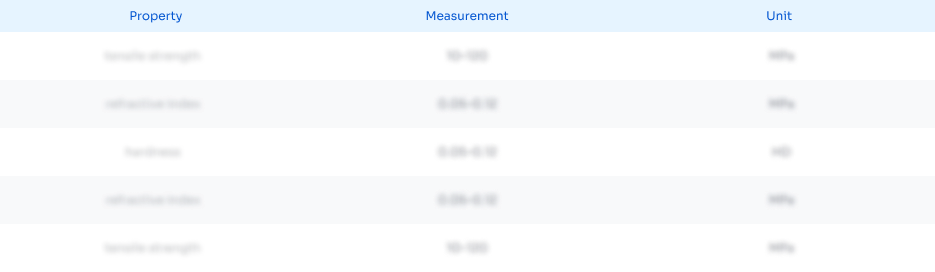
Abstract
Description
Claims
Application Information

- R&D Engineer
- R&D Manager
- IP Professional
- Industry Leading Data Capabilities
- Powerful AI technology
- Patent DNA Extraction
Browse by: Latest US Patents, China's latest patents, Technical Efficacy Thesaurus, Application Domain, Technology Topic, Popular Technical Reports.
© 2024 PatSnap. All rights reserved.Legal|Privacy policy|Modern Slavery Act Transparency Statement|Sitemap|About US| Contact US: help@patsnap.com