P-type Cu2.856In4Te8 base medium-high temperature thermoelectric material containing Sb and manufacturing technology thereof
A cu2.856in4te8, cu2.856sb0.6in4te8 technology, applied in the field of new materials, can solve the problems of insufficient performance of ternary semiconductors, low operating temperature, poor thermoelectric performance, etc., and achieve low cost, reliable operation and long life. Effect
- Summary
- Abstract
- Description
- Claims
- Application Information
AI Technical Summary
Problems solved by technology
Method used
Image
Examples
Embodiment 1
[0013] According to the chemical formula Cu 2.856 In 4 Te 8 The three-element particles of Cu, In and Te with a purity greater than 99.999wt.% are weighed and directly placed in a quartz tube for vacuum packaging. Then melt and synthesize at 850°C for 24 hours, then cool down to 390°C and anneal for 72 hours after melting and synthesis, crush and ball mill the annealed ingot. The ball milling time is controlled at 5 hours. Sintering, sintering time 8 minutes, sintering temperature 650 ° C, sintering pressure 55MPa, prepared Cu 2.856 In 4 Te 8 thermoelectric materials.
Embodiment 2
[0015] According to the chemical formula Cu 2.856 Sb 0.25 In 4 Te 8 Cu, Sb, In, and Te four-element particles with a purity greater than 99.999wt.% are weighed and directly placed in a quartz tube for vacuum packaging. Then melt and synthesize at 850°C for 24 hours, then cool down to 390°C and anneal for 72 hours after melting and synthesis, crush and ball mill the annealed ingot. The ball milling time is controlled at 5 hours. Sintering, sintering time 8 minutes, sintering temperature 650 ° C, sintering pressure 55MPa, prepared Cu 2.856 Sb 0.25 In 4 Te 8 thermoelectric materials.
Embodiment 3
[0017] According to the chemical formula Cu 2.856 Sb 0.5 In 4 Te 8 Cu, Sb, In, and Te four-element particles with a purity greater than 99.999wt.% are weighed and directly placed in a quartz tube for vacuum packaging. Then melt and synthesize at 850°C for 24 hours, then cool down to 390°C and anneal for 72 hours after melting and synthesis, crush and ball mill the annealed ingot. The ball milling time is controlled at 5 hours. Sintering, sintering time 8 minutes, sintering temperature 650 ° C, sintering pressure 55MPa, prepared Cu 2.856 Sb 0.5 In 4 Te 8 thermoelectric materials.
PUM
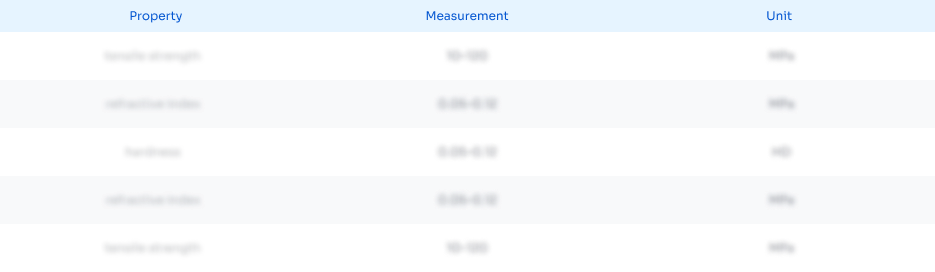
Abstract
Description
Claims
Application Information

- R&D
- Intellectual Property
- Life Sciences
- Materials
- Tech Scout
- Unparalleled Data Quality
- Higher Quality Content
- 60% Fewer Hallucinations
Browse by: Latest US Patents, China's latest patents, Technical Efficacy Thesaurus, Application Domain, Technology Topic, Popular Technical Reports.
© 2025 PatSnap. All rights reserved.Legal|Privacy policy|Modern Slavery Act Transparency Statement|Sitemap|About US| Contact US: help@patsnap.com