Method for preparing water gas from organic hazardous waste
A water gas and hazardous waste technology is applied in the field of using organic hazardous waste to prepare water gas, and can solve the problems of poor dioxin control effect, low treatment efficiency of organic hazardous waste, and inability to recycle and utilize resources.
- Summary
- Abstract
- Description
- Claims
- Application Information
AI Technical Summary
Problems solved by technology
Method used
Examples
Embodiment 1
[0025] The residue after the production and recovery of DMF solvent from synthetic leather is made to pH 7-9 by adding acid or alkali;
[0026] The raw coal is made into small pieces of fine coal through a rolling screen and a crusher; water and coal-water slurry additives are added, and the DMF residue is added according to the ratio of coal: DMF residue = 10:1. The liquid is stirred in the middle underground tank, passed through the vibrating screen, and the coal water slurry with a concentration of 55-65% is obtained, and is transported to the finished product tank by the slurry pump, stirred, and set aside;
[0027] The air is cryogenically separated by the air separation equipment to produce pure oxygen. After the oxygen is compressed, it passes through a special nozzle together with the coal water slurry and is sprayed into the gasifier. Gasification and cracking reactions to produce CO, CO 2 、H 2 , N 2 and hydrogen sulfide and other substances of water gas;
[0028]...
Embodiment 2
[0031] Waste solvents containing toluene, methyl ethyl ketone, ethyl acetate, xylene and corresponding paints, inks, paints and other substances are obtained from paint, ink, paint and other industries, and the ash content is controlled to be ≤ 10%;
[0032] The raw coal is made into pulverized coal with a mesh size of less than 200 through rolling screens and crushers;
[0033] The air is cryogenically separated by the air separation equipment to produce pure oxygen, and the compressed oxygen, water vapor, coal powder and waste solvent are sprayed into the gasifier through the respective / or the same nozzle, and the temperature is 1450~1550℃, 4.0~4.1 Gasification and cracking reactions are carried out under MPa high temperature and high pressure conditions to generate CO, CO 2 、H 2 , N 2 and hydrogen sulfide water gas;
[0034] High-temperature water gas (about 1350°C) enters the quenching chamber and is quenched by 250°C hot water to obtain water gas at 240°C and 3.9MPa. ...
Embodiment 3
[0037] Rectification waste obtained from pesticide production, with a fluorine content of ≤0.2%;
[0038] The raw coal is made into small pieces of fine coal through a rolling sieve and a crusher; add water and coal-water slurry additives, and add pesticide rectification residues according to the ratio of coal: pesticide distillation residues = 20:1, stir evenly, and send to The ball mill is ground into liquid, stirred in the middle underground tank, and passed through the vibrating screen to obtain a coal-water slurry with a concentration of 55-65%, which is transported to the finished product tank by a slurry pump, stirred, and set aside;
[0039] The air is cryogenically separated by air separation equipment to produce pure oxygen, and the compressed oxygen and coal-water slurry are sprayed into the gasifier through respective / or the same nozzle, and are heated at 1350-1450°C, 4.0-4.1MPa at high temperature and high pressure Gasification and cracking reactions are carried o...
PUM
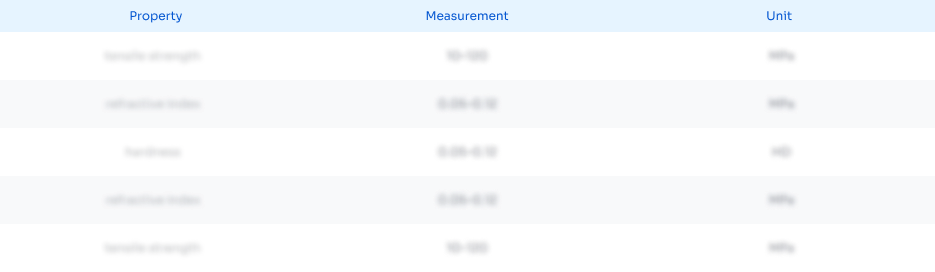
Abstract
Description
Claims
Application Information

- R&D
- Intellectual Property
- Life Sciences
- Materials
- Tech Scout
- Unparalleled Data Quality
- Higher Quality Content
- 60% Fewer Hallucinations
Browse by: Latest US Patents, China's latest patents, Technical Efficacy Thesaurus, Application Domain, Technology Topic, Popular Technical Reports.
© 2025 PatSnap. All rights reserved.Legal|Privacy policy|Modern Slavery Act Transparency Statement|Sitemap|About US| Contact US: help@patsnap.com