CVD preparation method of Co-doped MoS2 array in-situ electrodes
An in-situ electrode and array technology, applied in the field of in-situ electrode and its preparation, can solve the problems of inability to achieve vertical growth of molybdenum disulfide sheets, increase process complexity and cost, etc.
- Summary
- Abstract
- Description
- Claims
- Application Information
AI Technical Summary
Problems solved by technology
Method used
Image
Examples
Embodiment 1
[0022] At room temperature, dissolve cobalt chloride and molybdenum chloride in ethanol solution, wherein the concentration of cobalt chloride is 10mM, the concentration of molybdenum chloride is 290mM, and the ratio of cobalt atoms to the sum of the number of cobalt atoms plus molybdenum atoms is 5%. , through Ar gas and vacuum repeatedly three times to discharge the residual air in the tube furnace, then through Ar, the flow rate is 5SCCM, 0.2g of sulfur powder is placed on the upper part of the tube furnace, as the temperature in the tube furnace rises, the sulfur powder evaporates Sulfur vapors are formed. The precursor liquid was drop-coated on the surface of a flat graphite paper substrate, and dried on a hot table at 90°C for 10 min. Put the coated substrate into a tube furnace, react at 800°C for 30min under an Ar+S atmosphere, and take it out after natural cooling. figure 1 The SEM picture of this embodiment is shown, and it can be seen from the picture that a small ...
Embodiment 2
[0024] At room temperature, dissolve cobalt chloride and molybdenum chloride in ethanol solution, wherein the concentration of molybdenum chloride is 290mM, and the ratio of cobalt atoms to the sum of the number of cobalt atoms plus molybdenum atoms is 10%. The precursor liquid was drop-coated on the surface of a flat graphite paper substrate, and dried on a hot table at 90°C for 10 min. Put the coated substrate into the tube furnace, ventilate Ar gas and vacuumize repeatedly three times to discharge the residual air in the tube furnace, then pass Ar again, the flow rate is 2SCCM, 1g of sulfur powder is placed on the upper part of the tube furnace, along with the The temperature in the type furnace rises, the sulfur powder evaporates to form sulfur vapor, and reacts at 800°C for 30 minutes in an Ar+S atmosphere, and takes it out after natural cooling. figure 2 The SEM image of this embodiment is shown, and it can be seen from the figure that many nanosheets with a width of ~1...
Embodiment 3
[0026] At room temperature, dissolve cobalt chloride and molybdenum chloride in ethanol solution, wherein the concentration of molybdenum chloride is 290mM, and the ratio of cobalt atoms to the sum of the number of cobalt atoms plus molybdenum atoms is 15%. The precursor liquid was drop-coated on the surface of a flat graphite paper substrate, and dried on a hot table at 90°C for 10 min. Put the coated substrate into the middle of the tube furnace, and repeatedly discharge the residual air in the tube furnace with Ar gas and vacuumize it three times, then pass Ar again at a flow rate of 1 SCCM, put 0.5g of sulfur powder on the upper part of the tube furnace, and then As the temperature in the tube furnace rises, the sulfur powder evaporates to form sulfur vapor, react in an Ar+S atmosphere at 800°C for 30 minutes, and take it out after natural cooling. image 3 (a) shows the SEM image of this embodiment, from which it can be seen that many nanosheets with a width of 150-200 nm...
PUM
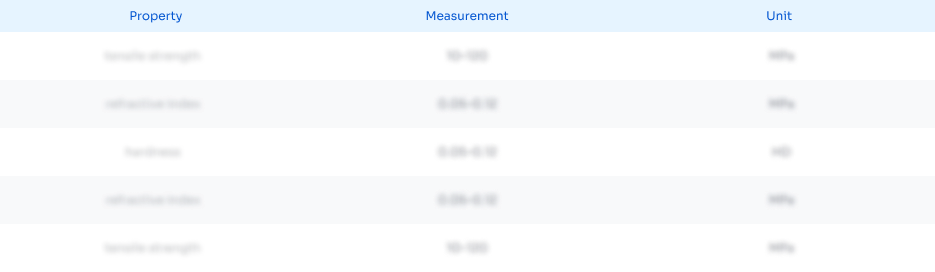
Abstract
Description
Claims
Application Information

- Generate Ideas
- Intellectual Property
- Life Sciences
- Materials
- Tech Scout
- Unparalleled Data Quality
- Higher Quality Content
- 60% Fewer Hallucinations
Browse by: Latest US Patents, China's latest patents, Technical Efficacy Thesaurus, Application Domain, Technology Topic, Popular Technical Reports.
© 2025 PatSnap. All rights reserved.Legal|Privacy policy|Modern Slavery Act Transparency Statement|Sitemap|About US| Contact US: help@patsnap.com