Bearing material obtained through loose sintering and having ultralow porosity and manufacturing method thereof
A technology of bearing material and manufacturing method, which is applied in the field of bearing materials, can solve the problems of unsatisfactory anti-fatigue strength and mechanical properties, and achieve the effect of meeting human health and environmental protection requirements, high mechanical strength, and excellent anti-fatigue performance
- Summary
- Abstract
- Description
- Claims
- Application Information
AI Technical Summary
Problems solved by technology
Method used
Image
Examples
Embodiment 1
[0065] Compared with Comparative Example 1 and Comparative Example 2, in Example 1, under the premise of the same ratio of different particle sizes, the mesh size of the small-particle spherical powder is reduced, so that the pores between the loosely packed spherical powders with larger particle sizes are closed. Smaller particle sizes for maximum packing, see image 3 . The porosity of the sintered body in Example 1 is reduced to below 1%, and the maximum size of a single pore is only 35um. With the decrease of the particle size ratio, the porosity and the maximum size of a single pore of the sintered body decrease rapidly. Experiments have proved that the mixture of copper alloy particles in the loose state is not pressed, but only through the matching and mixing of copper alloy particles of different meshes, a relatively dense sintered body can be obtained after sintering. Due to the high cost of the pressing equipment and the relatively complicated pressing process, espe...
PUM
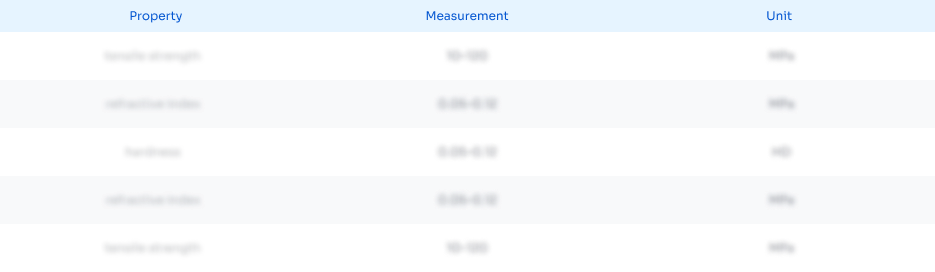
Abstract
Description
Claims
Application Information

- R&D Engineer
- R&D Manager
- IP Professional
- Industry Leading Data Capabilities
- Powerful AI technology
- Patent DNA Extraction
Browse by: Latest US Patents, China's latest patents, Technical Efficacy Thesaurus, Application Domain, Technology Topic, Popular Technical Reports.
© 2024 PatSnap. All rights reserved.Legal|Privacy policy|Modern Slavery Act Transparency Statement|Sitemap|About US| Contact US: help@patsnap.com