Aluminum alloy and preparation method thereof
A technology of aluminum alloy and aluminum alloy ingot casting, which is applied in the field of non-ferrous metals to achieve good anodic oxidation effect, bright and uniform surface color, and good mechanical properties
- Summary
- Abstract
- Description
- Claims
- Application Information
AI Technical Summary
Problems solved by technology
Method used
Image
Examples
preparation example Construction
[0029] In the preparation method of the aluminum alloy of the present invention, by adjusting the content of strengthening elements Mg, Si and Cu, the mechanical properties of the aluminum alloy are good and the anodic oxidation effect is good, and the surface color of the aluminum alloy is bright and uniform. Further, through the above-mentioned preparation method of aluminum alloy, the content and distribution of intermetallic compounds can be fully controlled, so that the aluminum alloy can obtain better mechanical properties and anodic oxidation effect.
[0030] The aluminum alloy raw materials mentioned in the present invention can be various pure metal ingots or alloy ingots containing Al, Mg, Mn, Cr, Ti, Si, Fe and Cu, without any particular limitation, as long as each group of the present invention can be obtained The mass percentage range of points is sufficient. There is no particular limitation on the method of making an aluminum alloy ingot from an aluminum alloy r...
Embodiment 1
[0036] The composition of aluminum alloy is calculated by mass percentage: Mg 0.50wt%, Si 1.20wt%, Cu 0.80wt%, Mn0.30wt%, Cr 0.20wt%, Ti 0.05wt%, Fe 0.15wt%;
[0037] According to the mass percentage of the above-mentioned aluminum alloy composition, calculate the quality of various master alloys or metal elements, and make aluminum alloy ingots from various master alloys or metal elements; ≤±15°C), heat preservation for 20 hours for homogenization annealing treatment; then place the uniformly annealed aluminum alloy ingot in an extruded rod and extrude it into an extruded material, the temperature of the extruded rod is 480°C, extruded The speed was 8 m / min, and the temperature of the extruded material was 500°C when it came out from the exit of the extruded rod; finally, it was kept at 170°C for 24 hours for aging treatment, and an aluminum alloy was prepared.
Embodiment 2
[0039] The composition of the aluminum alloy is calculated by mass percentage: Mg 1.20wt%, Si 0.45wt%, Cu 0.30wt%, Mn0.15wt%, Cr 0.10wt%, Ti 0.02wt%, Fe 0.12wt%;
[0040] According to the mass percentage of the above-mentioned aluminum alloy composition, the mass of various intermediate alloys or metal elements required is calculated, and various intermediate alloys or metal elements are made into aluminum alloy ingots; then the aluminum alloy ingots are heated at 590 ° C (temperature uniformity ≤±10°C), heat preservation for 5 hours for homogenization annealing treatment; then place the uniformly annealed aluminum alloy ingot in an extruded rod and extrude it into an extruded material, the temperature of the extruded rod is 540°C, extruded The speed was 8 m / min, and the temperature of the extruded material was 550°C when it came out of the exit of the extruded rod; finally, it was kept at 200°C for 12 hours for aging treatment, and an aluminum alloy was prepared.
PUM
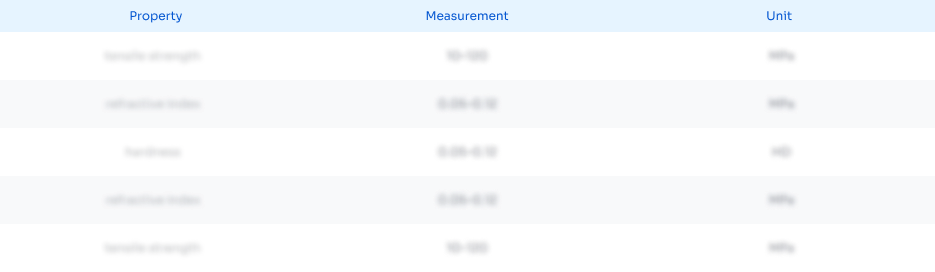
Abstract
Description
Claims
Application Information

- R&D
- Intellectual Property
- Life Sciences
- Materials
- Tech Scout
- Unparalleled Data Quality
- Higher Quality Content
- 60% Fewer Hallucinations
Browse by: Latest US Patents, China's latest patents, Technical Efficacy Thesaurus, Application Domain, Technology Topic, Popular Technical Reports.
© 2025 PatSnap. All rights reserved.Legal|Privacy policy|Modern Slavery Act Transparency Statement|Sitemap|About US| Contact US: help@patsnap.com