Method for producing wood plastic wallboard
A production method and technology of wood-plastic wall panels, applied in the field of architectural decorative wall panels, can solve the problems of single decoration, single heat preservation function, etc., and achieve the effects of reduced polarity, good compatibility, and low odor
- Summary
- Abstract
- Description
- Claims
- Application Information
AI Technical Summary
Problems solved by technology
Method used
Image
Examples
Embodiment 1
[0025] 1) Synthesis of modified functional materials: first dry calcium sulfate at 120°C to remove water, then weigh 99.5% of the dried calcium sulfate, 0.2% of aluminate coupling agent, 0.15% of stearic acid, and oxidize Polyethylene wax 0.15% is mixed in a high-speed mixer, and the temperature is gradually raised to 110°C to finally obtain a modified functional material;
[0026] 2) Plant fiber modification: crush the plant fiber, grind and sieve it into 100-mesh plant fiber powder, then dry at 110°C, add terpene resin accounting for 2% of the plant fiber mass and 1% aluminum acid during the drying process Ester coupling agent and 1% oxidized polyethylene wax to obtain modified plant fiber;
[0027] 3) Weigh 35% of waste plastics, 15% of modified plant fibers, 42.9% of modified functional materials, 1.7% of di-salt and tri-salt stabilizers, 0.8% of paraffin, 2.0% of reinforcing agent LDPE, and processing aids by weight percentage Add ACR-40 1.3%, foaming agent sodium lauryl...
Embodiment 2
[0029] 1) Synthesis of modified functional materials: first dry calcium sulfate at 120°C to remove water, then weigh 99.7% of the dried calcium sulfate, 0.2% of aluminate coupling agent, 0.05% of stearic acid, and oxidize Polyethylene wax 0.05% is mixed in a high-speed mixer, and the temperature is gradually raised to 100°C to finally obtain a modified functional material;
[0030] 2) Plant fiber modification: crush the plant fiber, grind and sieve it into 110-mesh plant fiber powder, then dry at 100°C, add 1% terpene resin and 1% aluminum acid to the plant fiber mass during the drying process Ester coupling agent and 0.5% oxidized polyethylene wax obtain modified plant fiber;
[0031] 3) Weigh 40% of waste plastics, 10% of modified plant fibers, 45% of modified functional materials, 1.2% of composite stabilizers, 0.3% of oxidized polyethylene wax, 1.2% of reinforcing agent HDPE, and processing aids by weight percentage Add ACR-2011.18%, foaming agent sodium lauryl sulfate 1....
Embodiment 3
[0033] 1) Synthesis of modified functional materials: first dry calcium sulfate at 120°C to remove water, then weigh 99.7% of the dried calcium sulfate, 0.1% of aluminate coupling agent, 0.1% of stearic acid, and oxidize Polyethylene wax 0.1% is mixed in a high-speed mixer, and the temperature is gradually raised to 100°C to finally obtain a modified functional material;
[0034]2) Plant fiber modification: crush the plant fiber, grind and sieve it into 110-mesh plant fiber powder, then dry at 100°C, add 1% terpene resin and 1% aluminum acid to the plant fiber mass during the drying process Ester coupling agent and 0.5% oxidized polyethylene wax obtain modified plant fiber;
[0035] 3) Take by weight 40% of waste plastics, 15% of modified plant fibers, 40% of modified functional materials, 1.5% of organotin stabilizers, 0.6% of oxidized polyethylene wax, 1.7% of reinforcing agent EVA, processing aids Add 0.5% agent CPE-135A, 0.5% foaming agent sodium lauryl sulfate, 0.15% col...
PUM
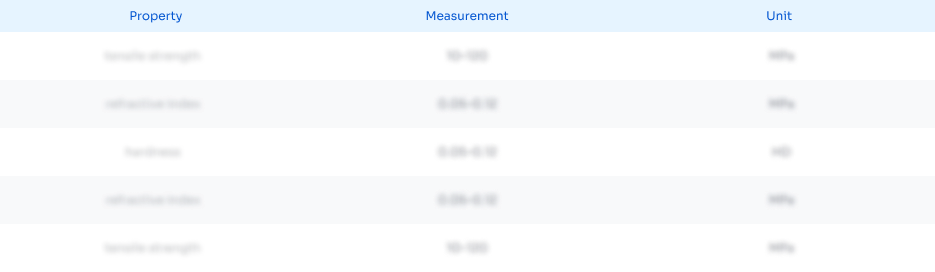
Abstract
Description
Claims
Application Information

- R&D
- Intellectual Property
- Life Sciences
- Materials
- Tech Scout
- Unparalleled Data Quality
- Higher Quality Content
- 60% Fewer Hallucinations
Browse by: Latest US Patents, China's latest patents, Technical Efficacy Thesaurus, Application Domain, Technology Topic, Popular Technical Reports.
© 2025 PatSnap. All rights reserved.Legal|Privacy policy|Modern Slavery Act Transparency Statement|Sitemap|About US| Contact US: help@patsnap.com