Laser ranging device and measuring and controlling method for plasma arc additive manufacturing of wires
A plasma arc and additive manufacturing technology, which is applied in plasma welding equipment, manufacturing tools, metal processing equipment, etc., can solve the problem of self-adjustment of welding torch, uncontrollable deposition process and deformation, accuracy and intuitiveness that cannot be compared with Compared with the precise laser displacement sensor, it achieves the effect of improving dimensional accuracy and molding quality, avoiding wire pressing, and precise molding process
- Summary
- Abstract
- Description
- Claims
- Application Information
AI Technical Summary
Problems solved by technology
Method used
Image
Examples
Embodiment 1
[0028] The present invention provides such figure 2 A measurement and control method for manufacturing a laser displacement sensing device using the above-mentioned wire plasma arc additive material is shown, and the specific implementation steps are as follows:
[0029] Step 1, before depositing, set the measuring position of the laser sensor 7, the welding torch 5, the laser displacement sensor 7 and the deposition body 3 are located on the same vertical plane, the measurement position of the laser displacement sensor 7 is located directly above the deposition body 3, and the laser displacement sensor The angle θ between 7 and the horizontal direction is 90°, and the initial distance L between the laser displacement sensor 7 and the location of the layup layer 1 60mm;
[0030] Step 2, the machine feeding mechanism and the wire reel 11 start to feed the wire, and after completing a deposition layer, move the laser displacement sensor 7 to the measurement position, the robot...
Embodiment 2
[0037] The present invention provides such figure 2 A measurement and control method for manufacturing a laser displacement sensing device using the above-mentioned wire plasma arc additive material is shown, and the specific implementation steps are as follows:
[0038]Step 1, before depositing, set the measuring position of the laser sensor 7, the welding torch 5, the laser displacement sensor 7 and the deposition body 3 are located on the same vertical plane, the measurement position of the laser displacement sensor 7 is located directly above the deposition body 3, and the laser displacement sensor The angle θ between 7 and the horizontal direction is 90°, and the initial distance L between the laser displacement measurement sensor 7 and the location of the layup layer 1 200mm;
[0039] Step 2, the machine feeding mechanism and the wire reel 11 start to feed the wire, and after completing a deposition layer, move the laser displacement sensor 7 to the measurement positio...
PUM
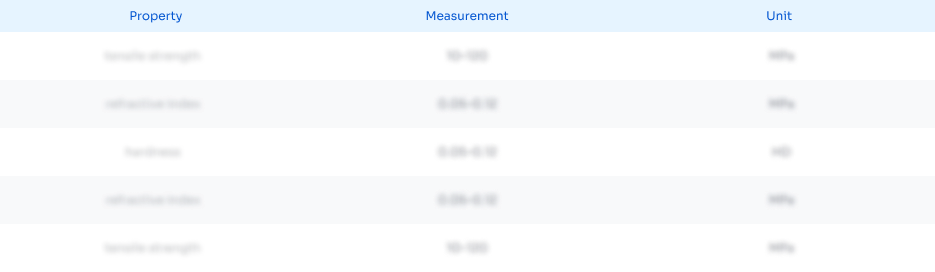
Abstract
Description
Claims
Application Information

- R&D Engineer
- R&D Manager
- IP Professional
- Industry Leading Data Capabilities
- Powerful AI technology
- Patent DNA Extraction
Browse by: Latest US Patents, China's latest patents, Technical Efficacy Thesaurus, Application Domain, Technology Topic, Popular Technical Reports.
© 2024 PatSnap. All rights reserved.Legal|Privacy policy|Modern Slavery Act Transparency Statement|Sitemap|About US| Contact US: help@patsnap.com