Preparation method for electroplating dehydrant
The technology of dehydrating agent and mass ratio is applied in the field of preparation of electroplating dehydrating agent, which can solve the problems of sweat spots, water droplets and poor macular, and achieve the effects of good water replacement performance, improved dehydration reaction activity, and good rust prevention performance.
- Summary
- Abstract
- Description
- Claims
- Application Information
AI Technical Summary
Problems solved by technology
Method used
Image
Examples
preparation example Construction
[0020] A preparation method of an electroplating dehydrating agent, comprising the steps of:
[0021] (1) Dry the peanut shells, crush them through a 160-mesh sieve, collect the sieved particles, take the sieved particles and add 15% sodium hydroxide solution at a mass ratio of 1:5, stir and mix at 20~25°C for 80~ After 90 minutes, the mixture was obtained. Take the mixture and add 30% 2,3-epoxypropyltrimethylammonium chloride aqueous solution according to the mass ratio of 5:3, stir and mix at 75~80°C for 2~3h, and cool to room temperature , dry, to obtain dry matter, and set aside;
[0022] (2) In terms of parts by mass, take 10~15 parts of heavy alkylbenzene, 7~9 parts of fatty acid chloride, 30~50 parts of dichloroethane, and 2~4 parts of anhydrous aluminum trichloride, mix them in 50~ Stir at 60°C for 3~4h to obtain the stirred mixture A, take the stirred mixture A and add chlorosulfonic acid at a mass ratio of 5:2, raise the temperature to 65~70°C and keep it for 1~2h, ...
Embodiment 1
[0029] A preparation method of an electroplating dehydrating agent, comprising the steps of:
[0030] (1) Dry the peanut shells, crush them through a 160-mesh sieve, collect the sieved particles, take the sieved particles and add 15% sodium hydroxide solution at a mass ratio of 1:5, stir and mix at 20°C for 80 minutes to obtain a mixture , take the mixture and add 30% 2,3-epoxypropyltrimethylammonium chloride aqueous solution according to the mass ratio of 5:3, stir and mix at 75°C for 2 hours, cool to room temperature, and dry to obtain a dried product for future use ;
[0031] (2) In parts by mass, mix 10 parts of heavy alkylbenzene, 7 parts of fatty acid chloride, 30 parts of dichloroethane, and 2 parts of anhydrous aluminum trichloride, and stir at 50°C for 3 hours to obtain a stirred mixture A. Take the stirred mixture A and add chlorosulfonic acid according to the mass ratio of 5:2, raise the temperature to 65°C and keep it for 1 hour, and adjust the pH to 7 to obtain t...
Embodiment 2
[0038] A preparation method of an electroplating dehydrating agent, comprising the steps of:
[0039] (1) Dry the peanut shells, crush them through a 160-mesh sieve, collect the sieved particles, take the sieved particles and add 15% sodium hydroxide solution at a mass ratio of 1:5, stir and mix at 25°C for 90 minutes to obtain a mixture , take the mixture and add 30% 2,3-epoxypropyltrimethylammonium chloride aqueous solution according to the mass ratio of 5:3, stir and mix at 80°C for 3 hours, cool to room temperature, and dry to obtain a dried product for future use ;
[0040] (2) In terms of parts by mass, take 15 parts of heavy alkylbenzene, 9 parts of fatty acid chloride, 50 parts of dichloroethane, and 4 parts of anhydrous aluminum trichloride, mix them, and stir at 60°C for 4 hours to obtain a stirred mixture A. Take the stirring mixture A and add chlorosulfonic acid according to the mass ratio of 5:2, raise the temperature to 70°C and keep it for 2 hours, and adjust t...
PUM
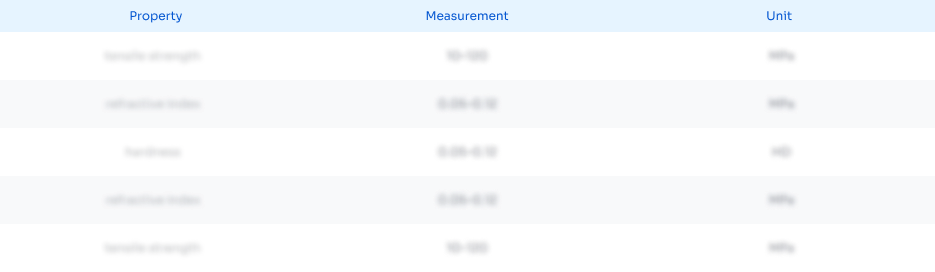
Abstract
Description
Claims
Application Information

- R&D
- Intellectual Property
- Life Sciences
- Materials
- Tech Scout
- Unparalleled Data Quality
- Higher Quality Content
- 60% Fewer Hallucinations
Browse by: Latest US Patents, China's latest patents, Technical Efficacy Thesaurus, Application Domain, Technology Topic, Popular Technical Reports.
© 2025 PatSnap. All rights reserved.Legal|Privacy policy|Modern Slavery Act Transparency Statement|Sitemap|About US| Contact US: help@patsnap.com