Clean coal reverse combustion hot blast stove
A reverse combustion and clean technology, applied in air heaters, fluid heaters, lighting and heating equipment, etc., can solve the problems of hot air temperature not keeping up, easy detonation hurting thermal efficiency, low utilization rate of combustion air, etc. The effects of energy saving, environmental protection, social benefits, comfortable operation and stable air output
- Summary
- Abstract
- Description
- Claims
- Application Information
AI Technical Summary
Problems solved by technology
Method used
Image
Examples
Embodiment Construction
[0010] The present invention will be further described below in conjunction with the accompanying drawings.
[0011] as attached figure 1 ~ attached image 3 As shown, the clean coal reverse combustion hot blast stove mainly includes a combustion chamber 1, fins 2, exhaust pipe 3 and coal bed 4.
[0012] The smoke exhaust pipe 3 is a vertically arranged corrosion-resistant metal round pipe. The outer wall of the smoke exhaust pipe 3 is fully welded and connected to many rectangular fins 2. The fins 2 are centered on the central axis of the smoke exhaust pipe 3 and radially distributed outwards in the radial direction. The thickness of the fins 2 is 0.1 mm to 1 mm. The inner vertical edge is on the outer wall of the smoke exhaust pipe 3 and parallel to the central axis of the smoke exhaust pipe 3, the outer vertical edge is on the upward extension surface of the side wall of the combustion chamber 1, and the bottom horizontal edge of the fin 2 is fully welded and connected to...
PUM
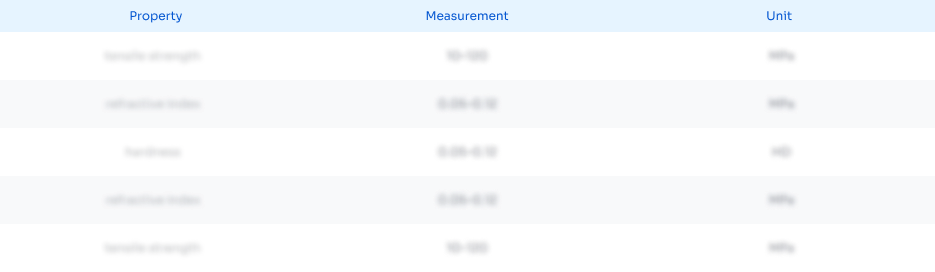
Abstract
Description
Claims
Application Information

- R&D Engineer
- R&D Manager
- IP Professional
- Industry Leading Data Capabilities
- Powerful AI technology
- Patent DNA Extraction
Browse by: Latest US Patents, China's latest patents, Technical Efficacy Thesaurus, Application Domain, Technology Topic, Popular Technical Reports.
© 2024 PatSnap. All rights reserved.Legal|Privacy policy|Modern Slavery Act Transparency Statement|Sitemap|About US| Contact US: help@patsnap.com