Method for reducing energy consumption of ferronickel production adopting RKEF technology
A ferronickel and process technology, applied in the field of metallurgy, can solve the problems of high energy consumption, achieve the effects of reducing the temperature required for smelting, reducing the existence of solid phase, and improving high-temperature flow properties
- Summary
- Abstract
- Description
- Claims
- Application Information
AI Technical Summary
Problems solved by technology
Method used
Image
Examples
Embodiment Construction
[0026] The present invention is further explained and illustrated below.
[0027] The present invention provides Examples 1, 2, 3 and Comparative Examples 1, 2. The slag composition includes the content of calcium oxide, aluminum oxide and ferrous oxide, the ratio of magnesium to silicon and the smelting temperature of slag are shown in Table 1. Reduction-electric furnace smelting to produce ferronickel.
[0028] The pre-reduction process parameters and process conditions of Examples 1, 2, and 3 are as follows: temperature 800-850° C., time 2-3 hours; pulverized coal injection amount is 8% of the dry ore mass, and bituminous coal dosage is 2% of the dry ore mass.
[0029] Examples 1, 2, and 3 smelting process parameters and process conditions are: temperature 1515-1550° C., time 2-3 hours; semi-coke dosage is 6% of dry ore mass.
[0030] The pre-reduction process parameters and process conditions of comparative examples 1 and 2 are: temperature 750-800° C., time 2-3 hours; co...
PUM
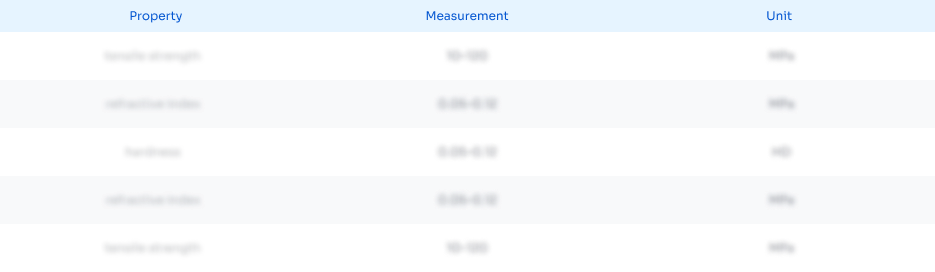
Abstract
Description
Claims
Application Information

- R&D
- Intellectual Property
- Life Sciences
- Materials
- Tech Scout
- Unparalleled Data Quality
- Higher Quality Content
- 60% Fewer Hallucinations
Browse by: Latest US Patents, China's latest patents, Technical Efficacy Thesaurus, Application Domain, Technology Topic, Popular Technical Reports.
© 2025 PatSnap. All rights reserved.Legal|Privacy policy|Modern Slavery Act Transparency Statement|Sitemap|About US| Contact US: help@patsnap.com