High-precision optical fiber cutting blade and machining method thereof
A technology of cutting blade and processing method, which is applied in the coupling of optical waveguide, etc., can solve the problems of fast wear and limited service life, and achieve the effects of good wear resistance, sharp cutting edge, and reduced micropores
- Summary
- Abstract
- Description
- Claims
- Application Information
AI Technical Summary
Problems solved by technology
Method used
Examples
Embodiment 1
[0045] A high-precision optical fiber cutting blade is composed of the following raw materials in parts by weight:
[0046] Tungsten carbide powder 80 parts
[0047] 8 parts cobalt powder
[0048] Beryllium 0.5 parts
[0049] Vanadium carbide 0.2 parts
[0050] 0.4 parts of chromium carbide.
[0051] S1: Weigh the raw materials of each component according to the requirements;
[0052] S2: Fully mix, put each component into a mixer for mixing, the mixer speed: 80rpm, time: 3h, to form a mixture A;
[0053] S3: crushing, put the mixture A into a superfine pulverizer for pulverization, the specification of the superfine pulverizer is 120-300 mesh, and obtain the mixture B;
[0054] S4: Primary drying, sieving and secondary drying, put the mixture B into the dryer for primary drying, the water content is 0.6-0.9%, then pass through a 150-300 mesh screen, and put it into the dryer again for further drying Secondary drying, the water content is 0.3-0.6%, and the mixture C is o...
Embodiment 2
[0064] A high-precision optical fiber cutting blade is composed of the following raw materials in parts by weight:
[0065] Tungsten carbide powder 85 parts
[0066] 9 parts cobalt powder
[0067] Beryllium 0.8 parts
[0068] Vanadium carbide 0.3 parts
[0069] 0.5 parts of chromium carbide.
[0070] S1: Weigh the raw materials of each component according to the requirements;
[0071] S2: Mix well, put each component into the mixer for mixing, mixer speed: 90rpm, time: 4h, to form mixture A;
[0072] S3: crushing, put the mixture A into a superfine pulverizer for pulverization, the specification of the superfine pulverizer is 120-300 mesh, and obtain the mixture B;
[0073] S4: Primary drying, sieving and secondary drying, put the mixture B into the dryer for primary drying, the water content is 0.6-0.9%, then pass through a 150-300 mesh screen, and put it into the dryer again for further drying Secondary drying, the water content is 0.3-0.6%, and the mixture C is obtain...
Embodiment 3
[0083] A high-precision optical fiber cutting blade is composed of the following raw materials in parts by weight:
[0084] Tungsten carbide powder 90 parts
[0085] 9 parts cobalt powder
[0086] Beryllium 1.0 parts
[0087] Vanadium carbide 0.4 parts
[0088] 0.5 parts of chromium carbide.
[0089] S1: Weigh the raw materials of each component according to the requirements;
[0090] S2: Mix well, put each component into the mixer for mixing, mixer speed: 110rpm, time: 4.5h, to form mixture A;
[0091] S3: crushing, put the mixture A into a superfine pulverizer for pulverization, the specification of the superfine pulverizer is 120-300 mesh, and obtain the mixture B;
[0092] S4: Primary drying, sieving and secondary drying, put the mixture B into the dryer for primary drying, the water content is 0.6-0.9%, then pass through a 150-300 mesh screen, and put it into the dryer again for further drying Secondary drying, the water content is 0.3-0.6%, and the mixture C is obtai...
PUM
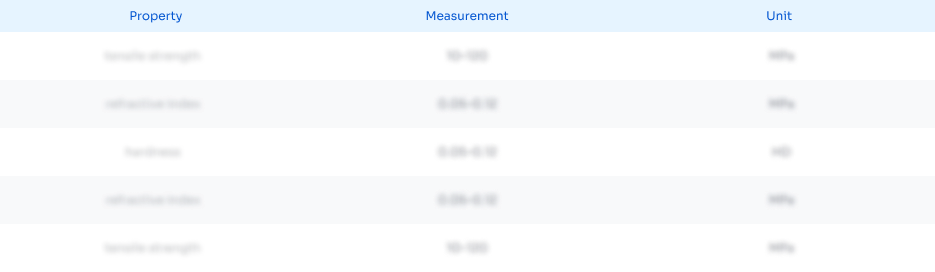
Abstract
Description
Claims
Application Information

- R&D
- Intellectual Property
- Life Sciences
- Materials
- Tech Scout
- Unparalleled Data Quality
- Higher Quality Content
- 60% Fewer Hallucinations
Browse by: Latest US Patents, China's latest patents, Technical Efficacy Thesaurus, Application Domain, Technology Topic, Popular Technical Reports.
© 2025 PatSnap. All rights reserved.Legal|Privacy policy|Modern Slavery Act Transparency Statement|Sitemap|About US| Contact US: help@patsnap.com