Wear-resistant anticorrosive coating, and preparation method and brushing method thereof
An anti-corrosion coating and brushing technology, which is applied in the direction of anti-corrosion coatings, fire-proof coatings, polyether coatings, etc., can solve the problems of heavy pipeline re-laying workload, pipeline corrosion, and pipeline scrapping, and achieves simple and easy preparation and coating methods line, maintain the effect of anti-corrosion ability
- Summary
- Abstract
- Description
- Claims
- Application Information
AI Technical Summary
Problems solved by technology
Method used
Image
Examples
Embodiment 1
[0046] The present embodiment provides a wear-resistant and anti-corrosion coating, and its preparation method is as follows:
[0047] Ingredients: 5g of carbon fiber, 5g of polyphenylene sulfide, 50g of additive, 80g of the first component, 100g of the second component and 50g of ceramic microbeads.
[0048] The additive is ethylene-methacrylic acid copolymer; the weight ratio of aromatic diamine and anti-aging additive in the first component is 1.5:2; the second component includes a silane coupling agent with a weight ratio of 1:2:2.4 , polyethylene glycol and epoxy resin.
[0049] When the wear-resistant and anti-corrosion coating is used, it is prepared on site, and its preparation and painting process steps are as follows:
[0050] Mix carbon fiber, molten polyphenylene sulfide, additives, first component, second component and ceramic microspheres in proportion, and immediately paint on the base material to be protected after mixing to complete the brushing.
Embodiment 2
[0052] The present embodiment provides a wear-resistant and anti-corrosion coating, and its preparation method is as follows:
[0053] Ingredients: 25g of carbon fiber, 25g of polyphenylene sulfide, 12g of sodium pyrophosphate, 10g of additives, 30g of the first component, 50g of the second component and 20g of ceramic beads.
[0054] The additive is a silicon-based oxide; the weight ratio of aromatic diamine and anti-aging additive in the first component is 1.5:1; the second component includes a silane coupling agent with a weight ratio of 1:2:1.5-2.3, Polyethylene glycol and epoxy resin.
[0055] When the wear-resistant and anti-corrosion coating is used, it is prepared on site, and its preparation and painting process steps are as follows:
[0056] Melt-blending polyethylene glycol and epoxy resin at a temperature of 150° C., and then adding a silane coupling agent therein to prepare the second component. Then mix carbon fiber, molten polyphenylene sulfide, sodium pyropho...
Embodiment 3
[0058] The present embodiment provides a wear-resistant and anti-corrosion coating, and its preparation method is as follows:
[0059] Ingredients: 8g of carbon fiber, 9g of polyphenylene sulfide, 23g of sodium polyacrylate, 13g of reactive flame retardant, 15g of additives, 40g of the first component, 60g of the second component and 25g of ceramic beads.
[0060] Wherein the reactive flame retardant is dibromoneopentyl glycol; additives include 10 g of ethylene-methacrylic acid copolymer and 5 g of ethylene-acrylic acid copolymer; the weight ratio of aromatic diamine and anti-aging additive in the first component is 1 : 1; the second component includes a silane coupling agent, polyethylene glycol and epoxy resin in a weight ratio of 1:2:2.1.
[0061] When the wear-resistant and anti-corrosion coating is used, it is prepared on site, and its preparation and painting process steps are as follows:
[0062] Melt-blending polyethylene glycol and epoxy resin at a temperature of 13...
PUM
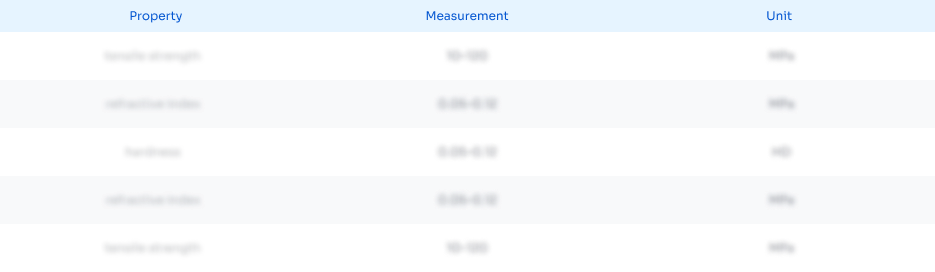
Abstract
Description
Claims
Application Information

- R&D
- Intellectual Property
- Life Sciences
- Materials
- Tech Scout
- Unparalleled Data Quality
- Higher Quality Content
- 60% Fewer Hallucinations
Browse by: Latest US Patents, China's latest patents, Technical Efficacy Thesaurus, Application Domain, Technology Topic, Popular Technical Reports.
© 2025 PatSnap. All rights reserved.Legal|Privacy policy|Modern Slavery Act Transparency Statement|Sitemap|About US| Contact US: help@patsnap.com