Method for regenerating FCC waste catalyst via microwave assistance
A waste catalyst, microwave-assisted technology, used in molecular sieve catalysts, chemical instruments and methods, catalyst regeneration/reactivation, etc., can solve the problems of no longer reuse, long operation time, complicated process, etc., to achieve structural integrity and recovery rate. High, simple processing effect
- Summary
- Abstract
- Description
- Claims
- Application Information
AI Technical Summary
Problems solved by technology
Method used
Image
Examples
Embodiment 1
[0020] Such as figure 1 Shown, this microwave-assisted regeneration FCC spent catalyst method, its specific steps are as follows:
[0021] Step 1. First, the spent FCC catalyst (chemical composition includes the following mass percentage components: Al25.95%, Si18.39%, Ce2.05%, La1.09%, V0.59%, Fe0.48%, Ni0. 56%) in a muffle furnace at 600°C for 1 hour, and then mixed with a sodium hydroxide solution with a concentration of 0.1mol / L according to a liquid-solid ratio of 5:1mL / g. After the microwave radiation power is 1600W, the microwave leaching temperature is Alkali leaching at 90°C for 30 minutes to obtain alkali leaching slag and vanadium-containing leaching solution; the removal rate of V after alkali leaching was 32.3%;
[0022] Step 2. Mix the alkali leaching slag obtained in step 1 with the hydrochloric acid solution with a concentration of 5wt% according to the liquid-solid ratio of 10:1mL / g, and then acid-leach for 30min under the conditions of microwave radiation po...
Embodiment 2
[0026] Such as figure 1 Shown, this microwave-assisted regeneration FCC spent catalyst method, its specific steps are as follows:
[0027] Step 1. First, the spent FCC catalyst (chemical composition includes the following mass percentage components: Al26.04%, Si18.69%, Ce2.01%, La1.11%, V0.59%, Fe0.46%, Ni0. 52%) in a muffle furnace at 600°C for 4 hours, and then mixed with a sodium hydroxide solution with a concentration of 0.5mol / L according to a liquid-solid ratio of 5:1mL / g. After the microwave radiation power is 1800W, the microwave leaching temperature is Alkali leaching at 100°C for 30 minutes yielded alkali leaching slag and vanadium-containing leaching solution; the removal rate of V after alkali leaching was 35.59%;
[0028] Step 2. Mix the alkali leaching slag obtained in step 1 with the hydrochloric acid solution with a concentration of 6wt% according to the liquid-solid ratio of 5:1mL / g, and then acid-leach for 20 minutes under the conditions of microwave radiati...
Embodiment 3
[0031] Such as figure 1 Shown, this microwave-assisted regeneration FCC spent catalyst method, its specific steps are as follows:
[0032] Step 1. First, the spent FCC catalyst (chemical composition includes the following mass percentage components: Al26.04%, Si18.69%, Ce2.01%, La1.11%, V0.59%, Fe0.46%, Ni0. 52%) in a muffle furnace at 700°C for 2 hours, and then mixed with a sodium hydroxide solution with a concentration of 0.8mol / L at a liquid-solid ratio of 15:1mL / g, then the microwave radiation power is 400W, and the microwave leaching temperature is Alkali leaching at 50°C for 60 minutes yielded alkali leaching slag and vanadium-containing leaching solution; the removal rate of V after alkali leaching was 27.7%;
[0033] Step 2. Mix the alkali leaching residue obtained in step 1 with the hydrochloric acid solution with a concentration of 1wt% according to the liquid-solid ratio of 3:1mL / g, and then acid-leach for 60min under the conditions of microwave radiation power of 4...
PUM
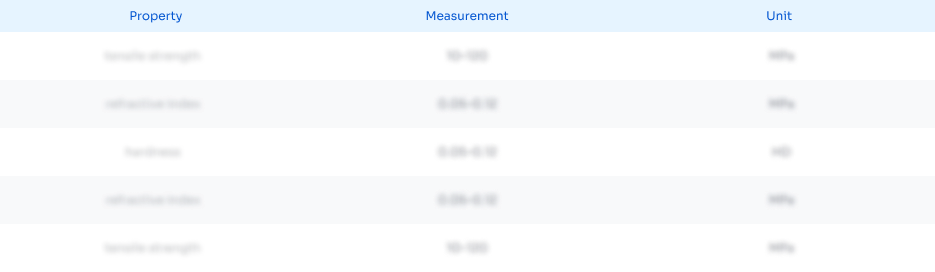
Abstract
Description
Claims
Application Information

- R&D Engineer
- R&D Manager
- IP Professional
- Industry Leading Data Capabilities
- Powerful AI technology
- Patent DNA Extraction
Browse by: Latest US Patents, China's latest patents, Technical Efficacy Thesaurus, Application Domain, Technology Topic, Popular Technical Reports.
© 2024 PatSnap. All rights reserved.Legal|Privacy policy|Modern Slavery Act Transparency Statement|Sitemap|About US| Contact US: help@patsnap.com