Composite cerium-iron-zirconium oxide catalyst, and preparation method and application thereof
A composite oxide and catalyst technology, which can be used in metal/metal oxide/metal hydroxide catalysts, physical/chemical process catalysts, preparation of carbon dioxide or inorganic carbonates, etc. To achieve the effect of easy regeneration and reuse, cheap and easy to obtain raw materials, and little environmental pollution
- Summary
- Abstract
- Description
- Claims
- Application Information
AI Technical Summary
Problems solved by technology
Method used
Examples
Embodiment 1
[0019] 1.20mmol Fe(NO 3 ) 3 9H 2 O, 2.76mmol ZrOCl 2 ·8H 2 O, 0.4mmol Ce(NO 3 ) 3 ·6H 2 O was dissolved in 200 mL of ethanol, and 10.00 mmol of citric acid was dissolved in 100 mL of ethanol. Add the ethanol solution of citric acid dropwise to the above salt solution (the volume ratio of the two solutions is 2:1). Stir the mixed solution at room temperature, evaporate the solvent to obtain the xerogel of cerium, iron and zirconium, dry it at 55°C to obtain the catalyst precursor, and finally roast the catalyst precursor at 300°C in the air to obtain 1%Ce-30%Fe-69%Zr solid solution catalyst.
[0020] Raw material methanol and dehydrating agent SiO 2 Added to the batch reactor, filled with CO 2 , under stirring conditions, heating to the temperature required for the reaction to carry out the synthesis reaction, after the reaction, the dehydrating agent and the catalyst are separated from the reaction product to obtain dimethyl carbonate. Methanol and CO 2 The conditi...
Embodiment 2
[0022] 3.30mmolFe(NO 3 ) 3 9H 2 O, 6.40 mmol ZrOCl 2 ·8H 2 O, 0.30 mmol Ce 2 (SO 4 ) 3 ·8H 2 O was dissolved in 100 mL of ethanol, and 40.00 mmol of citric acid was dissolved in 200 mL of ethanol. Add the citric acid ethanol solution dropwise to the above salt solution (the volume ratio of the two solutions is 1:2). Stir the mixed solution at room temperature, evaporate the solvent to obtain a xerogel of cerium, iron and zirconium, and dry it at 70° C. to obtain a catalyst precursor. Finally, the catalyst precursor was calcined at 400°C in air to obtain a 3%Ce-33%Fe-64%Zr solid solution catalyst. Add the raw materials and dehydrating agent into the batch reactor, fill with CO 2 , under stirring conditions, heating to the temperature required for the reaction to carry out the synthesis reaction, after the reaction, the dehydrating agent and the catalyst are separated from the reaction product to obtain dimethyl carbonate. Methanol and CO 2 The conditions for directl...
Embodiment 3
[0024] 16.20mmolFe(NO 3 ) 3 9H 2 O, 26.55mmolZr(NO 3 ) 4 ·5H 2 O, 2.25 mmol Ce 2 (SO 4 ) 3 ·8H 2 O was dissolved in 150 mL of ethanol, and 15.00 mmol of citric acid was dissolved in 150 mL of ethanol. Add the citric acid ethanol solution dropwise to the above salt solution (the volume ratio of the two solutions is 1:1). The mixed solution was stirred at room temperature, the solvent was evaporated to obtain a xerogel of cerium, iron and zirconium, and the catalyst precursor was obtained by drying at 80°C. Finally, the catalyst precursor was calcined at 500°C in air to obtain a 5%Ce-36%Fe-59%Zr solid solution catalyst. Add the raw materials and dehydrating agent into the batch reactor, fill with CO 2 , under stirring conditions, heating to the temperature required for the reaction to carry out the synthesis reaction, after the reaction, the dehydrating agent and the catalyst are separated from the reaction product to obtain dimethyl carbonate. Methanol and CO 2 The...
PUM
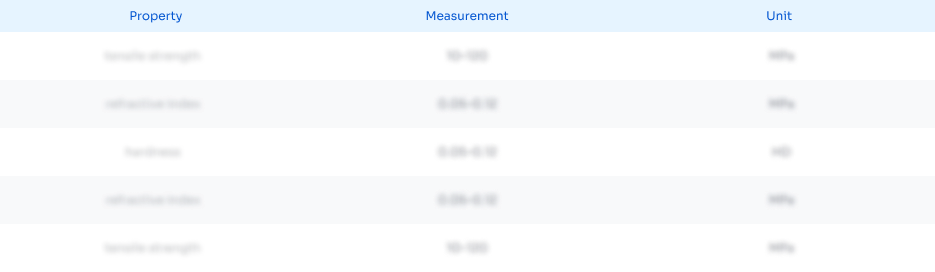
Abstract
Description
Claims
Application Information

- R&D
- Intellectual Property
- Life Sciences
- Materials
- Tech Scout
- Unparalleled Data Quality
- Higher Quality Content
- 60% Fewer Hallucinations
Browse by: Latest US Patents, China's latest patents, Technical Efficacy Thesaurus, Application Domain, Technology Topic, Popular Technical Reports.
© 2025 PatSnap. All rights reserved.Legal|Privacy policy|Modern Slavery Act Transparency Statement|Sitemap|About US| Contact US: help@patsnap.com