Alloy casting device and rotary continuous production equipment thereof
A technology of alloy casting and turntable, which is applied in casting equipment, equipment for feeding molten metal into molds, metal processing equipment, etc. It can solve the problems of chain casting equipment such as large mold loss, high powder rate, and large mold loss. Achieve the effects of high production efficiency, low powder rate and low loss rate
- Summary
- Abstract
- Description
- Claims
- Application Information
AI Technical Summary
Problems solved by technology
Method used
Image
Examples
Embodiment Construction
[0030] The present invention will be further described below in conjunction with embodiment.
[0031] An alloy casting device such as Figure 1-2 As shown, the flow distributor 1 and the condenser 3 are included, and the flow distributor 1 is arranged above the condenser 3 . The molten metal in the distributor 1 flows into the condenser 3 for cooling, and the casting of alloy or metal is completed. Wherein the condenser 3 can be set in the shape of a cylinder or a particle container as required, and is set according to the cast product.
[0032] The distributor 1 includes a cladding 1.1, a refractory material layer 1.2, a molten metal outlet 1.3, a switch 1.4, a liquid level detector 1.5 and a controller. The cladding 1.1 is configured as a container structure with a built-in depression and an open upper end. The refractory material layer 1.2 is arranged inside the cladding 1.1, and the molten metal outlet 1.3 is arranged at the bottom of the cladding 1.1. The switch 1.4 i...
PUM
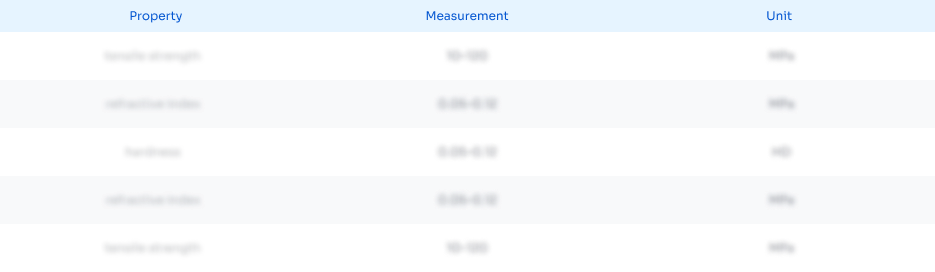
Abstract
Description
Claims
Application Information

- Generate Ideas
- Intellectual Property
- Life Sciences
- Materials
- Tech Scout
- Unparalleled Data Quality
- Higher Quality Content
- 60% Fewer Hallucinations
Browse by: Latest US Patents, China's latest patents, Technical Efficacy Thesaurus, Application Domain, Technology Topic, Popular Technical Reports.
© 2025 PatSnap. All rights reserved.Legal|Privacy policy|Modern Slavery Act Transparency Statement|Sitemap|About US| Contact US: help@patsnap.com