Force control method for robotic abrasive belt grinding machining for blade
A robot abrasive belt and grinding processing technology, which is applied in the direction of automatic grinding control device, abrasive belt grinder, workpiece feed motion control, etc. Overcome poor consistency, improve precision and surface quality, and achieve uniform removal
- Summary
- Abstract
- Description
- Claims
- Application Information
AI Technical Summary
Problems solved by technology
Method used
Image
Examples
Embodiment Construction
[0050]In order to make the object, technical solution and advantages of the present invention clearer, the present invention will be further described in detail below in conjunction with the accompanying drawings and embodiments. It should be understood that the specific embodiments described here are only used to explain the present invention, not to limit the present invention. In addition, the technical features involved in the various embodiments of the present invention described below can be combined with each other as long as they do not constitute a conflict with each other.
[0051] figure 1 It is a principle diagram of force control for blade robot abrasive belt grinding according to an embodiment of the present invention. Such as figure 1 As shown, in this embodiment, a blade robot abrasive belt grinding force control method specifically includes:
[0052] S101. The acquisition and monitoring of grinding force is used to convert the voltage signal acquired by the...
PUM
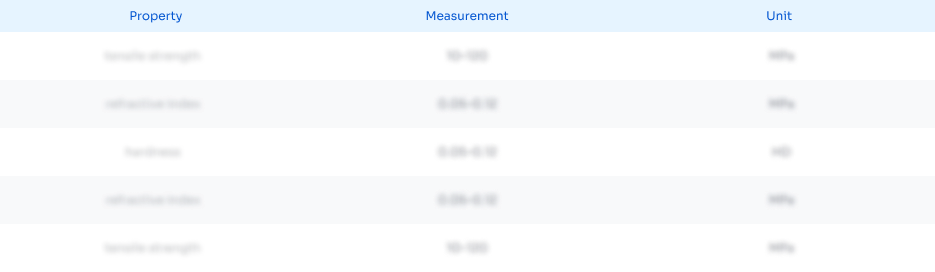
Abstract
Description
Claims
Application Information

- R&D
- Intellectual Property
- Life Sciences
- Materials
- Tech Scout
- Unparalleled Data Quality
- Higher Quality Content
- 60% Fewer Hallucinations
Browse by: Latest US Patents, China's latest patents, Technical Efficacy Thesaurus, Application Domain, Technology Topic, Popular Technical Reports.
© 2025 PatSnap. All rights reserved.Legal|Privacy policy|Modern Slavery Act Transparency Statement|Sitemap|About US| Contact US: help@patsnap.com