Technology for producing sodium bicarbonate and ammonium chloride by using triamine tail gas
A technology of baking soda and ammonium chloride, applied in the directions of ammonium chloride, ammonium halide, alkali metal chloride, etc., can solve the problems of poor crystallization quality of heavy alkali, increase of production cost, increase of loss, etc.
- Summary
- Abstract
- Description
- Claims
- Application Information
AI Technical Summary
Problems solved by technology
Method used
Image
Examples
Embodiment 1
[0073] All existing melamine plants in my country use the urea process. Except for several imported high-pressure process plants, other production plants use the normal pressure process (below 0.3 MPa) production technology developed by the country itself. Atmospheric pressure method is divided into different production processes such as one-step method and circulating carrier gas method. The normal pressure circulation method has the highest carbon dioxide content in the tail gas, and has the greatest impact on the control of the baking soda production process indicators. 2145kg of NH is produced per 1 ton of melamine produced by normal pressure circulation method 3 , CO 2 Mixed exhaust, where NH 3 The content is 994kg, CO 2 The content is 1130kg, the rest is inert gas, the temperature is 135-145°C, and the pressure is 0.15-0.3MPa(G).
[0074] Such as figure 1 As shown, the ammonia and carbon dioxide tail gas obtained from the production of melamine is passed into the tr...
Embodiment 2
[0090] Use urea as raw material to produce melamine by normal pressure circulation method, and produce 2200kg of NH for every 1t of melamine produced 3 , CO 2 Mixed exhaust, where NH 3 The content is 1019kg, CO 2 The content is 1159kg, the temperature is 135-145°C, and the pressure is 0.15-0.3MPa(G).
[0091] Pass the tail gas containing ammonia and carbon dioxide obtained from the production of melamine into the triamine tail gas ammonia absorption tower, absorb it with 35-40°C light ammonia brine from the deammonization tail gas ammonia suction tower, and obtain carbonated ammonia brine after cooling and clarification. Carbonated ammonia brine containing NaCl is 257.4~263.3g / L, FNH 3 / Na + 1.12~1.16, the temperature is 38~42°C, and the degree of carbonation of the carbonated ammonia brine should be controlled to be less than 80%, and the insufficient NH 3 Supplementation is regulated by the absorption of pure ammonia.
[0092] The carbonated ammonia brine is passed int...
PUM
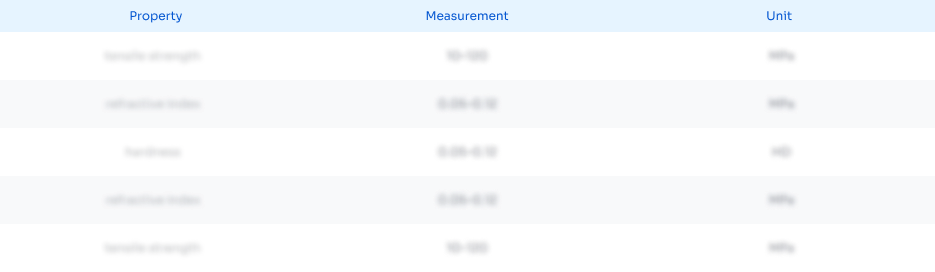
Abstract
Description
Claims
Application Information

- R&D
- Intellectual Property
- Life Sciences
- Materials
- Tech Scout
- Unparalleled Data Quality
- Higher Quality Content
- 60% Fewer Hallucinations
Browse by: Latest US Patents, China's latest patents, Technical Efficacy Thesaurus, Application Domain, Technology Topic, Popular Technical Reports.
© 2025 PatSnap. All rights reserved.Legal|Privacy policy|Modern Slavery Act Transparency Statement|Sitemap|About US| Contact US: help@patsnap.com