Anti-hydrogen corrosion-resistant coating and preparation method
A coating and corrosion-resistant technology, applied in the field of hydrogen-resistant and corrosion-resistant coatings and its preparation, can solve the problems of weak hydrogen resistance and hydrogen embrittlement, and achieve the effect of preventing hydrogen embrittlement, improving corrosion resistance and being easy to achieve.
- Summary
- Abstract
- Description
- Claims
- Application Information
AI Technical Summary
Problems solved by technology
Method used
Image
Examples
Embodiment 1
[0026] Raw materials: 31.75% of E44 epoxy resin, 34.29% of diluent, 0.09% of silane coupling agent KH550, 25.30% of polyamide 650 and 8.57% of sodium molybdate. Wherein, the diluent is made of 70% n-butanol and 30% xylene of the total diluent.
[0027] Preparation:
[0028] (1) Mix E44 epoxy resin and part of diluent according to mass percentage, add silane coupling agent KH550 and stir well, and prepare component A, wherein the addition of diluent accounts for 55% of the total diluent;
[0029] (2) Mix polyamide 650 with the remaining diluent to prepare component B;
[0030] (3) After adding sodium molybdate to component A and stirring, then add component B and mix well to obtain the coating.
[0031] Ordinary epoxy paint:
[0032] The basic steps are the same as in Example 1, except that sodium molybdate is not added to the raw materials. The specific component content is: 35.9% of E44 epoxy resin, 36.49% of diluent, 0.11% of silane coupling agent KH550 and 27.5% of poly ...
Embodiment 2
[0059] The basic steps are the same as in Example 1, except that the composition of the diluent is specifically (n-butanol 65% and xylene 35%), (n-butanol 75% and xylene 25%)
[0060] Coating the coating prepared in this embodiment on the surface of the substrate forms a hydrogen permeation barrier film, which can effectively reduce the hydrogen permeability, reduce or even prevent hydrogen embrittlement, and improve corrosion resistance.
Embodiment 3
[0062] Raw materials: 31% E51 epoxy resin, 32% diluent, 0.06% silane coupling agent KH550, 28% polyamide 593 and 8.94% ammonium molybdate. Wherein, the diluent is made of 70% n-butanol and 30% xylene of the total diluent.
[0063] Preparation:
[0064] (1) Mix E51 epoxy resin and part of the diluent according to the mass percentage, add the silane coupling agent KH550 and stir well, and prepare component A, wherein the addition of the diluent accounts for 52% of the total diluent;
[0065] (2) Mix the polyamide 593 with the remaining diluent to prepare component B;
[0066] (3) After adding ammonium molybdate to component A and stirring, then add component B and mix well to obtain the coating.
PUM
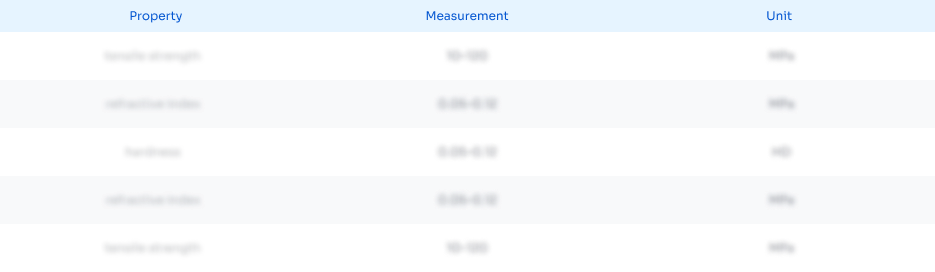
Abstract
Description
Claims
Application Information

- R&D Engineer
- R&D Manager
- IP Professional
- Industry Leading Data Capabilities
- Powerful AI technology
- Patent DNA Extraction
Browse by: Latest US Patents, China's latest patents, Technical Efficacy Thesaurus, Application Domain, Technology Topic, Popular Technical Reports.
© 2024 PatSnap. All rights reserved.Legal|Privacy policy|Modern Slavery Act Transparency Statement|Sitemap|About US| Contact US: help@patsnap.com