Vibration table substructure test method based on three-parameter control AMD
A technology of structural test and test method, which is applied in the field of structural test, can solve the problems of low control precision and high actuator stroke requirements, achieve the effects of low stroke requirements, reduce test cost, and improve test accuracy
- Summary
- Abstract
- Description
- Claims
- Application Information
AI Technical Summary
Problems solved by technology
Method used
Image
Examples
Embodiment Construction
[0033] In order to clearly and explicitly illustrate the principles, technical solutions and application effects of the present invention, the present invention will be described in detail below through specific examples. The embodiments provided here are only used to illustrate the purpose of the present invention, not to limit the technical solution of the present invention.
[0034] 1) Substructure splitting
[0035] refer to figure 1 , choose the 5-story shear frame structure as the test model, choose the bottom two-story structure as the experimental substructure 2, and the top three-story structure as the numerical substructure 3, the differential equation of motion of the overall structure 1 is shown in formula (1) :
[0036]
[0037] where m i , c i , k i , i=1,2...5 represent the lumped mass, interlayer damping coefficient and interlayer stiffness of each layer structure respectively, x i , are the displacement, velocity and acceleration of the correspondin...
PUM
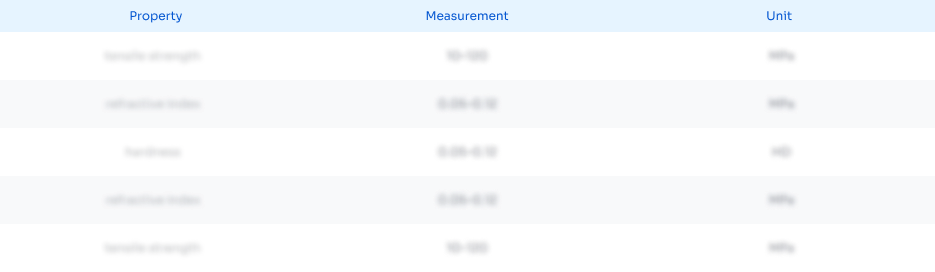
Abstract
Description
Claims
Application Information

- R&D
- Intellectual Property
- Life Sciences
- Materials
- Tech Scout
- Unparalleled Data Quality
- Higher Quality Content
- 60% Fewer Hallucinations
Browse by: Latest US Patents, China's latest patents, Technical Efficacy Thesaurus, Application Domain, Technology Topic, Popular Technical Reports.
© 2025 PatSnap. All rights reserved.Legal|Privacy policy|Modern Slavery Act Transparency Statement|Sitemap|About US| Contact US: help@patsnap.com