Energy recycling type temperature adjusting dehumidification sludge drying machine system
An energy recovery and sludge drying technology, applied in sludge treatment, water/sludge/sewage treatment, dehydration/drying/concentrated sludge treatment, etc., which can solve the problem of high energy consumption, safety risks, and working environment of drying workshop Poor and other problems, to achieve the effect of less wearing parts, long service life, and inhibiting the volatilization of volatile gases
- Summary
- Abstract
- Description
- Claims
- Application Information
AI Technical Summary
Problems solved by technology
Method used
Image
Examples
Embodiment
[0043] Such as figure 1 with figure 2 The shown works as follows:
[0044] 1. Material flow:
[0045] Sludge feed→Sludge feed strip cutter 37→First layer of mesh belt 32→Sludge strip crushing device 29→Second layer of mesh belt→Outlet (conveyor inlet).
[0046] 2. Cyclic drying process
[0047] 2.1 Circulating drying channel A: drying box 25 (air outlet) → plate filter 2 → bag filter 3 → No. 2 condenser 5 → circulating fan 18 → drying box air mixing space → air uniform plate → first layer of net Belt 32 → uniform air plate → drying box 25 (air outlet).
[0048] 2.2 Cycling dehumidification and drying channel B: drying box 25 (air outlet) → plate filter 2 → bag filter 3 → temperature-adjusting cooler 4 → heat recovery device 17 → No. 2 evaporator 16 → No. 1 evaporator 15 → Heat recovery device 17→No.1 condenser 6→Centrifugal fan without volute 7→Second layer air equalizing mesh belt 31→Air equalizing plate→Drying box air mixing space→Air equalizing plate→First layer mes...
PUM
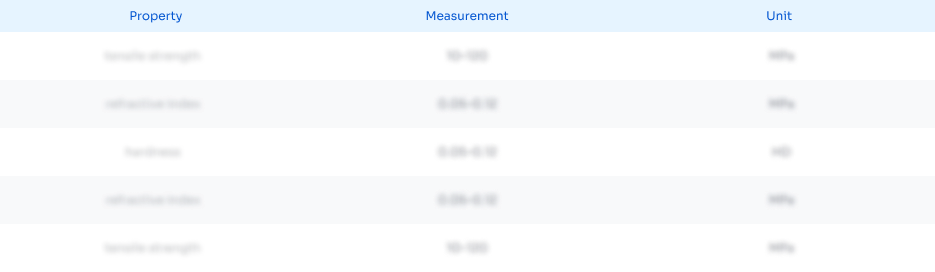
Abstract
Description
Claims
Application Information

- R&D
- Intellectual Property
- Life Sciences
- Materials
- Tech Scout
- Unparalleled Data Quality
- Higher Quality Content
- 60% Fewer Hallucinations
Browse by: Latest US Patents, China's latest patents, Technical Efficacy Thesaurus, Application Domain, Technology Topic, Popular Technical Reports.
© 2025 PatSnap. All rights reserved.Legal|Privacy policy|Modern Slavery Act Transparency Statement|Sitemap|About US| Contact US: help@patsnap.com