Method for recovering cassiterite from scheelite smelting slag
A technology for smelting slag and cassiterite, applied in chemical instruments and methods, wet separation, process efficiency improvement, etc., can solve the problems of metal loss, incompatibility, environmental damage, etc., and achieve less equipment, high recovery rate, investment low cost effect
- Summary
- Abstract
- Description
- Claims
- Application Information
AI Technical Summary
Problems solved by technology
Method used
Image
Examples
Embodiment 1
[0027] Mineral raw materials: select 50t / d (ton / day) scheelite smelting slag for industrial test, the particle size of the material is all -37 microns, the tin content is 0.42%, the gangue mineral calcium oxide content is 48.87%, and the fluorite content is 20.32% , 3.86% calcite, 1.09% chlorite, and 25.44% other minerals.
[0028] Recycle through the following specific steps:
[0029] (1) Add 60 g / t of sodium polyacrylate aqueous solution with a weight percent concentration of 1% to the mixing tank, stir for 40 minutes at a speed of 2200 rpm, and fully disperse the fine-grained cassiterite minerals;
[0030] (2) Use a water analyzer to classify the product of step (1) with a size of 19 μm, and put the fine-grained cassiterite of the product +19 μm into the fine mud shaker for two gravity separation operations to obtain tin coarse concentrate 1,-19 μm The fine-grained cassiterite is fed into the centrifugal concentrator for two gravity separation operations to obtain tin coar...
Embodiment 2
[0035] Mineral raw materials: select 100t / d scheelite smelting slag for industrial test, the particle size of the material is all -37 microns, the tin content is 0.81%, the gangue mineral calcium oxide content is 42.56%, the fluorite content is 18.52%, and the calcite content is 1.97%. The content of chlorite is 3.98%, and other minerals account for 32.97%.
[0036] Recycle through the following specific steps:
[0037] (1) Add 100g / t, 2% sodium polyacrylate aqueous solution by weight to the mixing tank, stir for 50 minutes at a speed of 2600 rpm, and fully disperse the fine-grained cassiterite minerals;
[0038] (2) Use a water analyzer to classify the product of step (1) with a size of 19 μm, and put the fine-grained cassiterite of the product +19 μm into the fine mud shaker for two gravity separation operations to obtain tin coarse concentrate 1,-19 μm The fine-grained cassiterite is fed into the centrifugal concentrator for two gravity separation operations to obtain tin ...
PUM
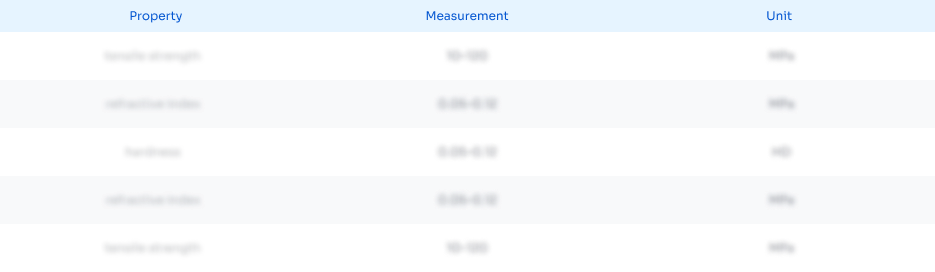
Abstract
Description
Claims
Application Information

- R&D Engineer
- R&D Manager
- IP Professional
- Industry Leading Data Capabilities
- Powerful AI technology
- Patent DNA Extraction
Browse by: Latest US Patents, China's latest patents, Technical Efficacy Thesaurus, Application Domain, Technology Topic, Popular Technical Reports.
© 2024 PatSnap. All rights reserved.Legal|Privacy policy|Modern Slavery Act Transparency Statement|Sitemap|About US| Contact US: help@patsnap.com