Preparation method of wear-resistant anti-skid speed bump material
A deceleration belt and anti-skid technology, which is applied in the field of deceleration belt preparation, can solve the problems of poor anti-skid performance and poor wear resistance, and achieve the effects of improving wear resistance and anti-skid performance, improving wear resistance, and enhancing compatibility
- Summary
- Abstract
- Description
- Claims
- Application Information
AI Technical Summary
Problems solved by technology
Method used
Examples
example 1
[0019] Put styrene-butadiene rubber, fluorosilicone rubber and sulfur into a mixer at a mass ratio of 3:2:1, and knead at 120°C for 1 hour to obtain a self-made vulcanized mixed rubber. Mesh sieve, collect the sieved river sand powder, mix the sieved river sand powder and silane coupling agent KH-570 at a mass ratio of 4:1 and stir for 10 minutes to obtain a mixture, and pour the mixture into a container with 6% of the mixture mass In the fermenter of beet oil and river bottom mud with 0.6% mixture mass, seal and ferment for 9 days at a temperature of 35°C. After the fermentation, take out the fermented product, wash the fermented product with deionized water, remove impurities, and let it dry naturally Dry, that is, modified river sand powder, put pyrophyllite and broken glass in a furnace at 1400 ° C for 2 hours to melt at a mass ratio of 2:1, and melt to obtain a molten liquid. After removing air bubbles, transport it to a porous bushing plate , at a speed of 2400r / min to d...
example 2
[0021] Put styrene-butadiene rubber, fluorosilicone rubber, and sulfur into a mixer at a mass ratio of 3:2:1, and knead at 140°C for 1.5 hours to obtain self-made vulcanized mixed rubber. Weigh 20g of river sand and grind for 7 minutes, then pass 100 mesh sieve, collect the sieved river sand powder, mix the sieved river sand powder and silane coupling agent KH-570 at a mass ratio of 4:1 and stir for 11 minutes to obtain a mixture, pour the mixture into the mixture with 6% of the mixture mass beet oil and 0.6% mixed mass of river bottom sludge in a fermenter, sealed and fermented at a temperature of 40°C for 10 days. After the fermentation, the fermentation product was taken out and washed with deionized water to remove impurities Dry it to get modified river sand powder. Put pyrophyllite and cullet in a kiln at 1500℃ to melt for 3 hours according to the mass ratio of 2:1, and melt to obtain a molten liquid. After removing air bubbles, transport it to the perforated bushing plat...
example 3
[0023] Put styrene-butadiene rubber, fluorosilicone rubber and sulfur into a mixer at a mass ratio of 3:2:1, and knead at 160°C for 2 hours to obtain a self-made vulcanized mixed rubber. Mesh sieve, collect the sieved river sand powder, mix the sieved river sand powder and silane coupling agent KH-570 at a mass ratio of 4:1 and stir for 12 minutes to obtain a mixture, pour the mixture into a container with 6% of the mixture mass In the fermenter of beet oil and river bottom mud with 0.6% mixture mass, seal and ferment at 45°C for 11 days. After the fermentation, take out the fermented product, wash the fermented product with deionized water, remove impurities, and let it dry naturally Dry, that is, modified river sand powder, put pyrophyllite and cullet in a kiln at 1600 ° C for 4 hours to melt at a mass ratio of 2:1, and melt to obtain a molten liquid. After removing air bubbles, transport it to a porous bushing plate , at a speed of 3000r / min to draw the wire, that is, self-...
PUM
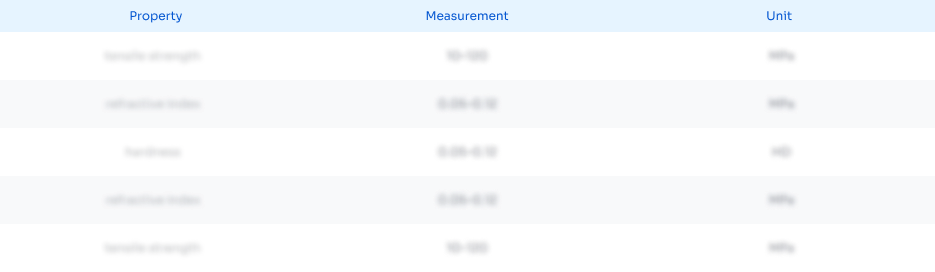
Abstract
Description
Claims
Application Information

- R&D
- Intellectual Property
- Life Sciences
- Materials
- Tech Scout
- Unparalleled Data Quality
- Higher Quality Content
- 60% Fewer Hallucinations
Browse by: Latest US Patents, China's latest patents, Technical Efficacy Thesaurus, Application Domain, Technology Topic, Popular Technical Reports.
© 2025 PatSnap. All rights reserved.Legal|Privacy policy|Modern Slavery Act Transparency Statement|Sitemap|About US| Contact US: help@patsnap.com