Autoclaved aerated concrete block and preparation method thereof
A concrete block and autoclaved aeration technology, which is applied to building components, buildings, building structures, etc., can solve the problems of poor product strength and frost resistance, unreasonable ratio of raw materials, and unsatisfactory quality of finished products. Achieve the effect of improving building energy-saving effect, saving land resources and easy processing
- Summary
- Abstract
- Description
- Claims
- Application Information
AI Technical Summary
Problems solved by technology
Method used
Image
Examples
Embodiment 1
[0027] An autoclaved aerated concrete block, which includes the following components in parts by weight: 86 parts of power plant bottom ash, 45 parts of river silt, 39 parts of tailings slag, 6 parts of cement, 15 parts of lime, and 3 parts of desulfurized gypsum 1.2 parts of aluminum powder, 0.3 parts of water-reducing agent, and 0.4 parts of water-retaining agent;
[0028] Wherein the power plant furnace bottom ash fineness 0.08mm hole sieve is 20%; the power plant furnace bottom ash includes the following components by weight percentage: silicon dioxide 52%, aluminum oxide 15%, iron oxide 2%, ferrous oxide 6 %;
[0029] Calcium oxide content in river silt is 94%, and the sieve residue of 0.08mm hole is 15%.
[0030] Among them, the water reducer is a polycarboxylate water reducer, which is prepared from 2 parts of polyethylene glycol monomethyl ether, 4-8 parts of unsaturated carboxylic acid, 7 parts of tartaric acid, and 10 parts of deionized water; Mix methyl cellulose ...
Embodiment 2
[0039] An autoclaved aerated concrete block, which comprises the following components in parts by weight: 72 parts of power plant bottom ash, 55 parts of river silt, 33 parts of tailings slag, 10 parts of cement, 18 parts of lime, and 4 parts of desulfurized gypsum 0.5 parts, aluminum powder 0.5 parts, water reducing agent 0.5 parts, water retaining agent 0.5 parts;
[0040] Wherein the power plant bottom ash fineness 0.08mm hole sieve is 15%; the power plant bottom ash includes the following components by weight percentage: silicon dioxide 45%, aluminum oxide 20%, iron oxide 3%, ferrous oxide 3% %;
[0041] The calcium oxide content in river silt is 86%, and the sieve residue of 0.08mm hole is 18%.
[0042] Among them, the water reducer is a polycarboxylate water reducer, which is prepared from 8 parts of polyethylene glycol monomethyl ether, 6 parts of unsaturated carboxylic acid, 8 parts of tartaric acid, and 5 parts of deionized water; Hydroxyl cellulose ether, hydroxypr...
Embodiment 3
[0051] An autoclaved aerated concrete block, which comprises the following components in parts by weight: 80 parts of power plant bottom ash, 65 parts of river silt, 35 parts of tailings slag, 5 parts of cement, 20 parts of lime, and 2 parts of desulfurized gypsum 0.8 parts of aluminum powder, 0.7 parts of water reducing agent, and 0.2 parts of water retaining agent;
[0052] Among them, the power plant bottom ash with a fineness of 0.08mm hole sieve is 18%; the power plant bottom ash includes the following components by weight percentage: 50% silicon dioxide, 23% aluminum oxide, 1% iron oxide, and 5% ferrous oxide. %;
[0053] Calcium oxide content in river silt is 90%, and the sieve residue of 0.08mm hole is 12%.
[0054] Among them, the water reducer is a polycarboxylate water reducer, which is prepared from 10 parts of polyethylene glycol monomethyl ether, 4-8 parts of unsaturated carboxylic acid, 6 parts of tartaric acid, and 8 parts of deionized water; Mix methyl cellu...
PUM
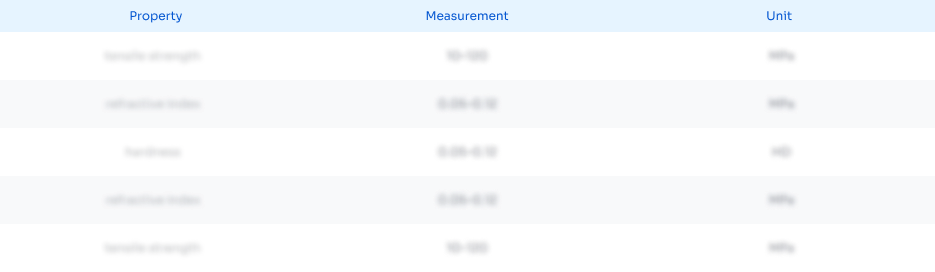
Abstract
Description
Claims
Application Information

- R&D
- Intellectual Property
- Life Sciences
- Materials
- Tech Scout
- Unparalleled Data Quality
- Higher Quality Content
- 60% Fewer Hallucinations
Browse by: Latest US Patents, China's latest patents, Technical Efficacy Thesaurus, Application Domain, Technology Topic, Popular Technical Reports.
© 2025 PatSnap. All rights reserved.Legal|Privacy policy|Modern Slavery Act Transparency Statement|Sitemap|About US| Contact US: help@patsnap.com