3D printing building material
A building material and 3D printing technology, applied in the field of 3D printing, can solve the problem that the compressive strength cannot meet the demand, achieve good compressive strength, reduce dehydration costs and energy consumption, and have high density
- Summary
- Abstract
- Description
- Claims
- Application Information
AI Technical Summary
Problems solved by technology
Method used
Examples
Embodiment 1
[0016] A 3D printing building material, its raw materials include by weight: 110 parts of aggregate, 65 parts of cinder, 4 parts of pottery clay, 15 parts of asbestos, 5 parts of desulfurized gypsum, 6 parts of titanium diboride, 1 part of copper sulfate, and adhesive 6 parts, 1 part calcium nitrate, 2 parts potassium carbonate, 1 part silver nitrate, 50 parts water.
Embodiment 2
[0018] A 3D printing building material, its raw materials include by weight: 120 parts of aggregate, 45 parts of cinder, 12 parts of pottery clay, 5 parts of asbestos, 15 parts of desulfurized gypsum, 1 part of titanium diboride, 2 parts of copper sulfate, and adhesive 2 parts, 2 parts of calcium nitrate, 1 part of potassium carbonate, 2 parts of silver nitrate, 30 parts of water.
[0019] The aggregate includes by weight: 35 parts of yellow sand, 30 parts of silicomanganese slag, 15 parts of construction waste, and 40 parts of graphite powder compound. The adhesion agent includes by weight: 1 part of condensed sodium silicate, 1.2 parts of monolauryl phosphate, and 1 part of sodium oleate.
[0020] The graphite powder composite is prepared by the following process: mix disproportionated rosin, graphite powder, dibutyltin dilaurate, and toluene diisocyanate, heat up and stir under nitrogen protection, add epoxy soybean oil and mix evenly, add phthalic anhydride, N, Mix N-dime...
Embodiment 3
[0022] A 3D printing building material, its raw materials include by weight: 112 parts of aggregate, 60 parts of cinder, 6 parts of pottery clay, 12 parts of asbestos, 8 parts of desulfurized gypsum, 4 parts of titanium diboride, 1.2 parts of copper sulfate, adhesive 5 parts, 1.2 parts of calcium nitrate, 1.7 parts of potassium carbonate, 1.4 parts of silver nitrate, 45 parts of water.
[0023] The aggregate includes by weight: 45 parts of yellow sand, 20 parts of silicomanganese slag, 35 parts of construction waste, and 20 parts of graphite powder compound. The adhesion agent includes by weight: 3 parts of condensed sodium silicate, 0.5 part of monolauryl phosphate, and 2 parts of sodium oleate.
[0024] The graphite powder composite is prepared by the following process: mix disproportionated rosin, graphite powder, dibutyltin dilaurate, and toluene diisocyanate, heat up to 90°C and stir for 40 minutes under nitrogen protection, add epoxy soybean oil and mix evenly, add phtha...
PUM
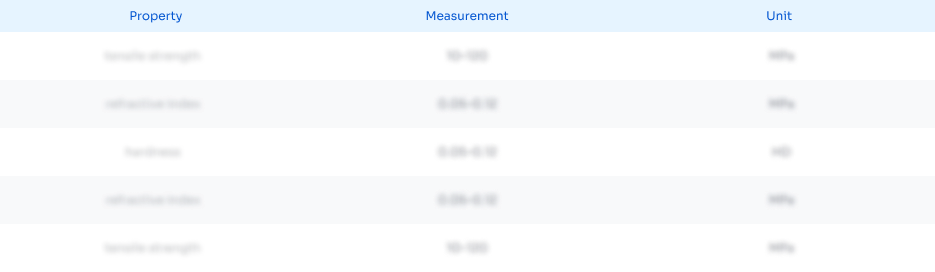
Abstract
Description
Claims
Application Information

- Generate Ideas
- Intellectual Property
- Life Sciences
- Materials
- Tech Scout
- Unparalleled Data Quality
- Higher Quality Content
- 60% Fewer Hallucinations
Browse by: Latest US Patents, China's latest patents, Technical Efficacy Thesaurus, Application Domain, Technology Topic, Popular Technical Reports.
© 2025 PatSnap. All rights reserved.Legal|Privacy policy|Modern Slavery Act Transparency Statement|Sitemap|About US| Contact US: help@patsnap.com