Pressed glass lamp cup, preparation method thereof and lamp
A technology for pressing glass and lamp cups, used in lighting and heating equipment, coatings, portable lighting devices, etc., can solve the problems of low entry probability of material molecules, inability to complete crystallization and film formation, and high product prices, and achieve simple equipment and solutions. Internal conduction problem, good insulation effect
- Summary
- Abstract
- Description
- Claims
- Application Information
AI Technical Summary
Problems solved by technology
Method used
Image
Examples
preparation example Construction
[0052] Correspondingly, the present invention also provides a method for preparing a pressed glass lamp cup, comprising:
[0053] (1) Mix component A, component B and thinner to obtain an insulating coating. After mixing component A, component B and diluent, it is also necessary to perform bubble removal treatment on the insulating coating to avoid bubbles during film formation.
[0054] (2) Dip or spray the insulating paint on the inner surface of the pressed glass lamp cup body, and then perform leveling treatment.
[0055] Dip coating and spray coating adopt different methods for different product specifications and comprehensive output efficiency. For example, when it is applied to PAR lamps, the spray coating process is used; when it is applied to MR16, GU10 and other spotlights, the dip coating process is used.
[0056] (3) drying the glass;
[0057] Specifically, step (3) includes:
[0058] First dry in the low temperature zone of 50-70 degrees for 2-7 minutes; then ...
Embodiment 1
[0065] (1) Production component A: 5% pyromellitic dianhydride, 35% diaminodiphenyl ether, 40% organosilane, 5% 3-aminopropyltrimethoxysilane, β-(3,4- Epoxycyclohexyl) ethyltrimethoxysilane 5%, ethyl orthosilicate 5%, ethyl acetate 5% are mixed according to the proportion;
[0066] (2) Making component B: mixing 60% of siloxane oligomer, 20% of metal oxide catalyst, and 20% of structure control agent according to the proportion;
[0067] (3) Mix component A and component B at a ratio of 100:5 to obtain an insulating coating;
[0068] (4) Dip-coat the insulating paint on the inner surface of the pressed glass lamp cup body, and then perform leveling treatment;
[0069] (5) Dry the glass in a low temperature zone of 50 degrees for 5 minutes; then dry it in a medium temperature zone of 90 degrees for 6 minutes; finally dry it in a high temperature zone of 140 degrees for 10 minutes;
[0070] (6) The glass is forcedly air-cooled until it reaches normal temperature.
Embodiment 2
[0072] (1) Production component A: 10% pyromellitic dianhydride, 25% diaminodiphenyl ether, 30% organosilane, 5% 3-aminopropyltrimethoxysilane, β-(3,4- Epoxycyclohexyl) ethyl trimethoxysilane 10%, ethyl orthosilicate 10%, ethyl acetate 10% mixed according to the proportion;
[0073] (2) Preparation of component B: mix 70% of siloxane oligomer, 15% of metal oxide catalyst, and 15% of structure control agent according to the proportion;
[0074] (3) Mix component A and component B at a ratio of 100:7 to obtain an insulating coating;
[0075] (4) Dip-coat the insulating paint on the inner surface of the pressed glass lamp cup body, and then perform leveling treatment;
[0076] (5) Dry the glass in a low temperature zone of 60 degrees for 4 minutes; then dry it in a medium temperature zone of 100 degrees for 5 minutes; finally dry it in a high temperature zone of 150 degrees for 8 minutes;
[0077] (6) The glass is forcedly air-cooled until it reaches normal temperature.
PUM
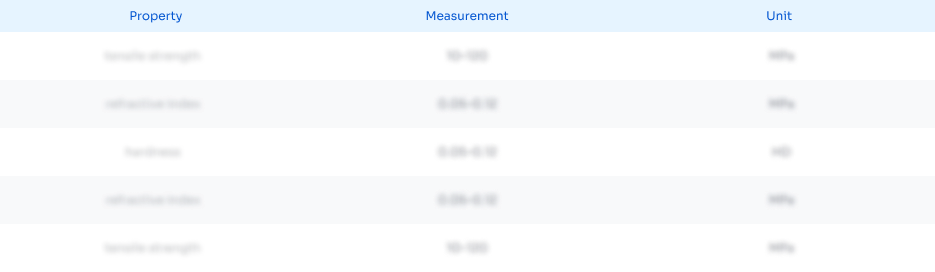
Abstract
Description
Claims
Application Information

- Generate Ideas
- Intellectual Property
- Life Sciences
- Materials
- Tech Scout
- Unparalleled Data Quality
- Higher Quality Content
- 60% Fewer Hallucinations
Browse by: Latest US Patents, China's latest patents, Technical Efficacy Thesaurus, Application Domain, Technology Topic, Popular Technical Reports.
© 2025 PatSnap. All rights reserved.Legal|Privacy policy|Modern Slavery Act Transparency Statement|Sitemap|About US| Contact US: help@patsnap.com