Method for conducting production through nickel smelting slag
A technology for smelting slag and slag, which is applied in the field of metallurgical production using nickel smelting slag, and can solve problems such as difficulty in handling copper oxide ore.
- Summary
- Abstract
- Description
- Claims
- Application Information
AI Technical Summary
Problems solved by technology
Method used
Examples
Embodiment 1
[0213] A method of producing from nickel smelting slag, comprising the steps of:
[0214] Step 1, slag mixing:
[0215] The molten nickel smelting slag obtained from the slag outlet of the smelting furnace in the "matte-making process" process is fed into the DC electric arc furnace, and lime and SiO are added at the same time 2 , MgO, Al 2 o 3 , forming a mixed slag, and adding copper sulfide concentrate and nickel oxide concentrate at the same time; heating the mixed slag to a molten state to form a reaction slag, and allowing the reaction slag to achieve natural mixing; real-time monitoring of the reaction slag, through regulation and control Guarantee the two parameters (a) and (b) to obtain the slag after the reaction; corresponding to (a): the temperature of the reaction slag is 1660°C, use a refractory spray gun to insert into the reaction slag, and use nitrogen as the loading gas. Spray copper slag, copper-containing soot, miscellaneous copper and copper-containing ...
Embodiment 2
[0219] A method of producing from nickel smelting slag, comprising the steps of:
[0220] Step 1, slag mixing:
[0221] Put the molten nickel smelting slag obtained from the slag outlet of the blowing furnace in the "copper matte converting" process into the pourable smelting reaction slag tank, and add limestone, dolomite, red mud, FeO and Fe at the same time 2 o 3 , forming a mixed slag, adding copper oxide concentrate and nickel sulfide concentrate at the same time; using oxygen-enriched air, injecting natural gas, anthracite and coke particles with a particle size of 20mm, heating the mixed slag to a molten state, and forming a copper-containing reaction slag ;Real-time monitoring of the reaction slag, by adjusting and controlling the two parameters (a) and (b) at the same time, to obtain the slag after the reaction is completed;
[0222] Corresponding to (a) the temperature of copper-containing reaction slag is 1660°C, insert a refractory spray gun into the reaction sla...
Embodiment 3
[0240] A method of producing from nickel smelting slag, comprising the steps of:
[0241] Step 1, slag mixing: the molten nickel smelting slag obtained from the blowing slag of the "copper matte nickel blowing" process through the slag outlet of the depletion furnace is added to the AC electric arc furnace, and limestone and high-calcium red mud after desodiumization are added at the same time to form Mix the slag, add copper oxide concentrate and copper sulfide concentrate at the same time; use oxygen with a preheating temperature of 600°C, inject anthracite, coke particles and coal powder with a particle size of 20mm, heat the mixed slag to a molten state, and form a The copper reaction slag is mixed by mechanical stirring; the reaction slag is monitored in real time, and the two parameters (a) and (b) are guaranteed at the same time through regulation to obtain the slag after the reaction is completed;
[0242] Corresponding to (a): the temperature of copper-containing reac...
PUM
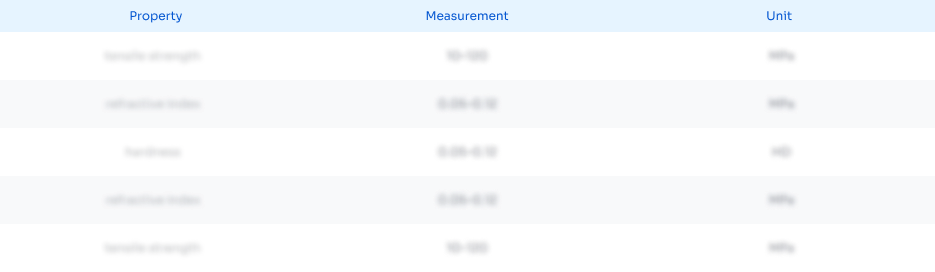
Abstract
Description
Claims
Application Information

- Generate Ideas
- Intellectual Property
- Life Sciences
- Materials
- Tech Scout
- Unparalleled Data Quality
- Higher Quality Content
- 60% Fewer Hallucinations
Browse by: Latest US Patents, China's latest patents, Technical Efficacy Thesaurus, Application Domain, Technology Topic, Popular Technical Reports.
© 2025 PatSnap. All rights reserved.Legal|Privacy policy|Modern Slavery Act Transparency Statement|Sitemap|About US| Contact US: help@patsnap.com