Preparation method of nano-composite ultrafine heavy calcium carbonate
A heavy calcium carbonate, nano-composite technology, applied in the direction of calcium carbonate/strontium/barium, nanotechnology, nanotechnology, etc., can solve the problems of poor binding force, can not be used as functional materials, low viscosity, etc., to achieve large BET, flow And the effect of good extrudability and uniform particle size distribution
- Summary
- Abstract
- Description
- Claims
- Application Information
AI Technical Summary
Problems solved by technology
Method used
Image
Examples
Embodiment 1
[0027] A preparation method of nanocomposite superfine ground calcium carbonate, comprising the steps of:
[0028] (1) Take light-burned and medium-burned calcium oxide to remove impurities and digest it to obtain Ca(OH) with a concentration of 30% and an activity of 40s 2 Suspension, standing and aging for 72h, separating and removing impurities, and finally obtaining Ca(OH) with a concentration of 5%. 2 seminal plasma suspension and indigestible limestone nuclei;
[0029] (2) Coarsely grind the limestone core first, then add grinding and dispersing agent, wet grind the limestone core to become ultrafine heavy calcium slurry with d95≤2μm, the crystal shape is spherical or quasi-spherical, and the obtained ultrafine heavy calcium slurry Dilute the material to a concentration of 10%; the grinding dispersant is a mixture of polycarboxylate sodium salt neutral dispersant and polycarboxylate sodium hydrochloric acid dispersant in a mass ratio of 1:1, and the amount added is based...
Embodiment 2
[0036] A preparation method of nanocomposite superfine ground calcium carbonate, comprising the steps of:
[0037] (1) Take calcium oxide to remove impurities and digest it to obtain Ca(OH) with a concentration of 20% and an activity of 50s 2 Suspension, standing and aging for 46h, separating and removing impurities, and finally obtaining Ca(OH) with a concentration of 8%. 2 seminal plasma suspension and indigestible limestone nuclei;
[0038] (2) Coarsely grind the limestone core first, then add grinding and dispersing agent, wet grind the limestone core to become ultrafine heavy calcium slurry with d95≤2μm, the crystal shape is spherical or quasi-spherical, and the obtained ultrafine heavy calcium slurry Dilute the material to a concentration of 15%; the grinding dispersant is a mixture of polycarboxylate sodium salt neutral dispersant and polycarboxylate sodium hydrochloric acid dispersant in a mass ratio of 1:1, and the amount added is based on the ultrafine weight Add 1...
Embodiment 3
[0045] A preparation method of nanocomposite superfine ground calcium carbonate, comprising the steps of:
[0046] (1) Take calcium oxide to remove impurities and digest it to obtain Ca(OH) with a concentration of 25% and an activity of 30s 2 Suspension, standing and aging for 16h, separating and removing impurities, and finally obtaining Ca(OH) with a concentration of 6%. 2 seminal plasma suspension and indigestible limestone nuclei;
[0047] (2) Coarsely grind the limestone core first, then add grinding and dispersing agent, wet grind the limestone core to become ultrafine heavy calcium slurry with d95≤2μm, the crystal shape is spherical or quasi-spherical, and the obtained ultrafine heavy calcium slurry The material is diluted to a concentration of 13%; the grinding dispersant is a mixture of polycarboxylate sodium salt neutral dispersant and polycarboxylate sodium hydrochloric acid dispersant in a mass ratio of 1:1, and the amount of addition is based on ultrafine weight ...
PUM
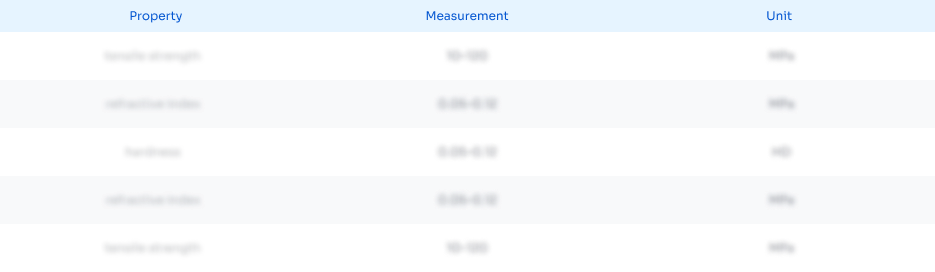
Abstract
Description
Claims
Application Information

- R&D
- Intellectual Property
- Life Sciences
- Materials
- Tech Scout
- Unparalleled Data Quality
- Higher Quality Content
- 60% Fewer Hallucinations
Browse by: Latest US Patents, China's latest patents, Technical Efficacy Thesaurus, Application Domain, Technology Topic, Popular Technical Reports.
© 2025 PatSnap. All rights reserved.Legal|Privacy policy|Modern Slavery Act Transparency Statement|Sitemap|About US| Contact US: help@patsnap.com